アシスト蒸着法
アシスト蒸着法は、基板に付着しない第三の材料を用いて主要蒸着材料の蒸着レートや結晶性を高める方法。有機薄膜太陽電池の有機半導体膜蒸着工程では共蒸発分子誘起結晶化法と呼ばれ、n型とp型有機半導体を共蒸着しながら、基板に付着しない共蒸発分子としてポリジメチルシロキサン(PDMS)などの液体分子を同時蒸発させて有機半導体分子に衝突させすることにより有機半導体の結晶化を誘起する。つまり、有機半導体の結晶性を高める狙いがあり、とくに光電流の生成が大幅に向上するといわれる。この方法は共蒸着膜だけでなく、p層、n層の単層蒸着膜でも有効で、グレインサイズが増加するとされる。 |
アズデポ状態
起源はas deposition。成膜直後の状態、つまり成膜後にアニールなどの後処理をしていない状態。
|
穴埋め法(別名:はんだ剥離法)
サブトラクト法で両面PCBを製造する際に用いられる手法で、テンティング法と対峙する手法。この手法では基材にスルーホールを開けた後、Cuを両面にめっき成膜し、穴埋め用インクをスルーホールに埋め込む。この後、サブトラクト法でCu膜をパターニングし、最後にDFRとともにインクを除去する。テンティング法と違い、確実にスルーホールをエッチング工程から保護することができる反面、その分工程が多くなる。
※ステラ・コーポレーションではPCB製造向けとしてCAD/CAMソフトウェア「Stella Vision」、測長&外観検査装置「STシリーズ/LSTシリーズ」を製品化しています。
|
イオン液体
液体で存在する塩をいう。通常、塩は食塩のように常温下では固体だが、塩を構成するイオンを比較的サイズの大きなある種の有機イオンに置換した場合、融点が低くなり、室温付近でも液体状態で存在することがある。イオン液体は蒸気圧が非常に低く、大気中では加熱してもほとんど蒸発しない。一方、減圧環境下では安定な液体状態を維持する反面、加熱すると容易に蒸発させることができる。このため、イオン液体中に低分子有機半導体を真空蒸着すると、単結晶の有機半導体が得られる。
|
イオン化ポテンシャル
原子、イオンなどから電子を取り去ってイオン化するために必要なエネルギー。ある原子がその電子をどれだけ強く結びつけているのかの目安を意味する。単位はeV。
|
イオン注入
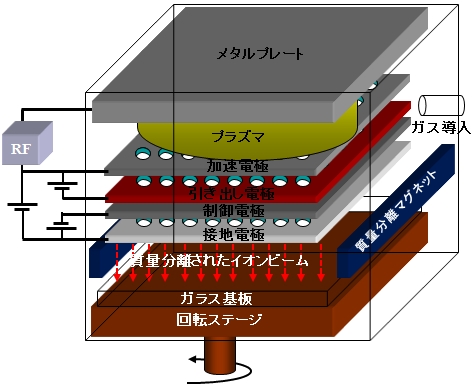 |
▲質量分離型イオン注入装置のイメージ |
物質のイオンを固体に注入する加工法。おもな目的は別の元素を注入することにより対象物質に化学的変化を与えるとともに、物質の破損または破壊など構造的な変化も与えて固体特性を変化させることで、半導体やpoly-Si TFTで用いられる。
半導体ではボロン、リン、砒素など純度の高いドーパント原子をドープする。ドーパント原子のボロンは三フッ化ホウ素(BF3)ガス、リンはホスフィン(PH3)ガス、砒素はアルシン(AsH3)ガスが用いられ、数keVからMeV級のエネルギーで加速する。注入の結果、半導体中にキャリアとして電子または正孔が作られ、半導体の伝導性を変化させる。
poly-Si TFTでは、Pチャネルを作製する際にソース/ドレイン領域に高濃度のボロンを注入する。一方、Nチャネルを作製する際はソース/ドレイン領域にホスフィンPH3を用いて高濃度リンを注入する。
低温poly-Si TFTでは従来、大面積へのイオンビーム照射が比較的容易な非質量分離型のイオンドーピング装置が用いられてきたが、近年はトランジスタ特性向上のため、半導体と同様、必要なイオンのみを照射すべく質量分離型のドーピング装置が用いられている。 |
異方導電フィルム(ACF)
ACFはICの多ピン化や狭ピッチ化にともない従来のワイヤーボンド方式に代わる接続方式で、熱硬化型エポキシ樹脂の中に導電性の粒子を分散させたフィルム。ディスプレイパネルとドライバICを接続する場合、図のようにTAB、COF、COG側の端子とガラス基板上のITOパッドでACFを挟む。この結果、端子間に挟まれた導電性ボールだけが潰れて電気的に接続される仕組み。
|
インセルタッチ
LCDパネル内にタッチパネル機能をインテグレーションしたもの。完成したタッチパネルをカバーガラスとLCDパネルの間に配置する通常の外付け型に比べ、パネルが薄型軽量化できるほか、製造コストも総じて抑制できる。画素TFTやドライバ回路だけでなく、タッチパネル機能もビルトインできる低温poly-Si TFT-LCDならではの付加価値といえる。
|
ALD(Atomic Layer Deposition)
プリカーサ原料Aと酸化原料または窒化原料Bを交互に真空チャンバ内に供給して酸化膜や窒化膜を1原子層づつ成膜する手法。代表的な成膜対象であるSiO2膜の場合、アミノシランを導入して下地に吸着し排気した後、オゾンまたはラジカル酸素で酸化させて排気する。一方、Al2O3膜はTMA(トリメチルアルミニウム)を原料ガスに用い、同じくオゾンまたはラジカル酸素で酸化する。これらプリカーサ原料Aを導入し酸化ガスBを投入するというフローを1サイクルに設定。原子をいくつ積むかによってサイクル数を設定する。1サイクルは数秒で、サイクル数と膜厚は完全にリニアな関係になる。このため、膜厚ユニフォミティが高く、Ra=0.1nmクラスというフラットサーフェースが得られる。成膜温度は200℃以下で、成膜温度と膜質にはほとんど相関がなく、成膜温度を上げるとサイクルタイムが短くなる。
そのメカニズムからスループットが低いのが弱点で、100nmオーダーの膜厚では1時間程度かかる。このため、膜質を重視する用途、言い換えれば成膜レートが低くても許容される用途に適したデポジション法といえる。
|
エキシマレーザーアニール(ELA)法
低温poly-Si TFT-LCDでa-Siプリカーサ膜を結晶化する際に標準的に用いられる。XeCl(波長308nm)またはKrF(248nm)の高パワーエキシマレーザー(出力300Wクラス)を照射することでa-Siを溶融再結晶化してpoly-Si膜にする。現時点ではラインビームによるスキャン方式が一般的である。
アニール工程は結晶性を左右するキープロセスであり、結晶性が上がればモビリティも向上する。グレインサイズを大きくすることで、結晶粒界の欠陥を相対的に低減させるアプローチが一般的だ。レーザーアニールはa-Si膜を一旦溶かしてから再結晶させるが、冷却時に膜の体積が増えるため、結晶と結晶の間で隆起が発生し、これが欠陥となりVthのバラつきを引き起こすと考えられている。近年ではこの冷却速度を緩和するために、レーザーをパルスレーザーからCWレーザー(連続波)に変える試みもある。
従来、ELA装置のラインビーム長は465oが最長で、この結果、対応基板サイズは2スキャン仕様で第4世代(730×920o)がマックスだった。しかし、2011年にラインビーム650oの第6世代対応装置(1500×1850o)が登場。1スキャンで最大59型パネルが製造できるようになった。さらに、2013年にビーム長1100〜1300oの第8世代対応装置(2160×2400o)が開発されるなど、従来から低温poly-Si TFT-LCDの弱点とされてきた基板サイズの制約は解消されつつある。 |
Agナノワイヤーインク
太さがnmオーダーのワイヤー状Agを主成分にしたインク。このインクを基板上に塗布すると、ナノAgワイヤーがランダムネットワークもしくは自己整合的に配列したマトリクスネットワークを形成する。このため、電極として機能する。
有力用途は透明電極で、パターニングの開口率次第によって光透過特性と表面抵抗が決まる。つまり、要求されるスペックによってこれらを自在に設定することができる。もちろん、フレキシブル性にも優れる。パターニング法はコンベンショナルなフォトリソを用いるのが一般的だが、インクジェットプリンティング法などでダイレクト印刷することも原理的には可能だ。
|
エッチングばらつき
エッチングはスピードでプロセスが調整されるが、エッチングシャワーを通る際に、進行方法のXYや基板中央部と基板端によっても、液の流れや溜りなどによりバラつきが発生する。例えば、写真のように隙間があり液通りが良い箇所はエッチング速度が速くなり、結果的に細りやすくなる。これに対し、隙間がなく液通りが悪い箇所はエッチング速度が遅くなり、太りやすくなる。このため、あらかじめCADデータ上で補正を行っておくエッチング補正が不可欠となっている。
※ステラ・コーポレーションのCAD/CAMソフトウェア「Stella Vision」 ではエッチング補正機能を搭載しています。
|
Nd:YAGレーザー
YAG結晶を製造する過程でイットリウム(Y)を数%のネオジム(Nd)でドープした結晶を用いるYAGレーザー。基本波(第一高調波)は1064nm、第二高調波は532nm(グリーンレーザー)、第三高調波は355nm(UVレーザー)。デバイスの研究開発、リペア、産業機器や医療用機器に広く用いられる。
|
FTO
フッ素をドープした酸化錫で、ITOに代わる安価な透明導電膜として注目されている。化学的安定性、機械的強度、耐熱性に優れるため、色素増感型太陽電池、薄膜太陽電池、キャパシタ、省エネルギーウィンドウなどの用途が挙げられる。ただ、基本的に導電率と可視光透過率はトレードオフの関係になる。
|
円筒形ターゲット(ロータリーターゲット)方式
スパッタリング成膜時におけるターゲットの利用効率を高めるために開発されたターゲット方式。図のように円筒形ターゲットを円回転させる仕組みで、回転によってターゲットのエロージョンが均一化されるため利用効率が70〜80%に向上する。コンベンショナルなプレーナーターゲットはカソードの背後にエロージョンを均一化させる揺動マグネット機構を設けても利用率は最大40%に過ぎず、2倍前後という高い利用効率が得られる。このため、ここにきてとくに高価で資源枯渇が懸念されるITOの成膜で採用する動きが顕在化している。
|
ODF(One Drop Fill)法:液晶滴下法
LCDの液晶注入法のひとつ。TFTアレイ基板とカラーフィルター(CF)基板を貼り合わせる前に液晶材料を片方の基板に滴下して貼り合わせて切断する手法で、従来の真空注入法に比べ大幅なタクトタイム短縮が見込める。このため、近年はこの工程においてデファクトスタンダードとなっている。
液晶滴下方式と従来の真空注入方式の違いは、CF側に設けられた柱状スペーサーにある。液晶滴下方式では、あらかじめCF側に柱状スペーサー(ポストスペーサーとも呼ばれる)が設けられているため、従来のセル工程からスペーサーボール散布工程をレス化できる。もちろん、液晶材料を真空注入していた時間も大幅に短縮されるため、生産性も大幅に向上する。フローは@UV硬化型シール材ディスペンス塗布する(本シール、ダミーシール)、A大気中で液晶滴下する、B真空中で両面基板を貼り合わせる、Cシール材をUV硬化させる、といった仕組みで、セルギャップは液晶充填量で決まる。つまり、液面高さで決まるため、過不足なく充填するにはディスペンサの吐出量制御が重要になる。
|
OD(Optical Density)値
黒色度を示す指標で、透過率と対比する用語。0〜6の6段階で表し、1は透過率100%、6は透過率0.0001%である。フォトマスクの遮光膜やカラーフィルターのブラックマトリクスといった遮光用途では4もしくは5が求められる。
|
オフセットスクリーン印刷法
コンベンショナルなスクリーン印刷法を改良したメソッド。いうまでもなく、通常のスクリーン印刷は基板上に直接ペーストを印刷するのに対し、オフセットスクリーン印刷ではPDMS(ジメチルポリシロキサン)ブランケット上にペーストを印刷した後、このPDMSブランケットを基板に接触させて転写する。この際、PDMSブランケットがペーストに含まれる溶剤を吸収するため、基板への転写時にペーストのにじみが少なくなり、印刷解像度が向上する。さらに、PDMSブランケットの存在によって基板上にスクリーンマスクのメッシュ痕もほとんど残らない。もちろん、厚膜化が容易というスクリーン印刷の特徴は兼ね備える。
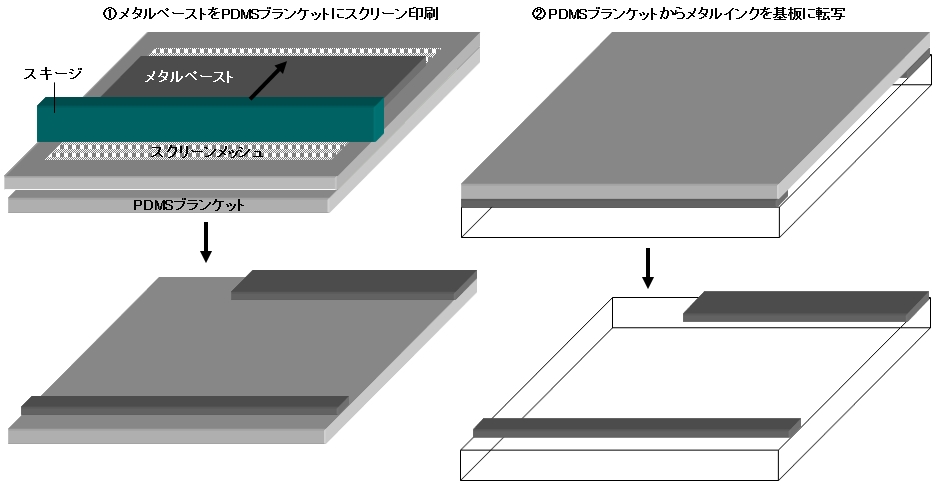 |
▲オフセットスクリーン印刷法によるゲート電極形成イメージ
|
|
加圧焼成法
インク・ペーストを硬化させる方法のひとつで、コンベンショナルなμmサイズ粒子インク・ペーストを印刷した後、焼成時にメカニカル圧力をかけることで焼成温度を抑制する。詳細は明らかにされていないが、150℃以下の焼成でもメタル粒子を凝集させることができ、圧力レスに比べシート抵抗値が3桁も低下するといわれる。いうまでもなく、低温プロセスが求められるフレキシブルデバイス、とくに有機TFTに有効とされる。
|
会合体
会合は同種の分子2個以上が比較的弱い分子間力によって集合し、一つの単位として行動している状態。こうした単位を会合体という。会合体を構成している分子の数(会合度)によって二量体、三量体とも呼ぶ。会合を起こす分子は水やアルコールのように水酸基を持つものが多い。
|
回折格子
格子状のパターンによる回折を利用して干渉縞を作るために使用される光学素子。格子パターンは、直線状の凹凸がμmサイズ周期やnmサイズ周期で平行に並んで構成されていることが多い。
|
カソードセパレータ方式
パッシブマトリクス駆動有機ELディスプレイや調色/調光型フルカラー有機EL照明パネルのカソードをパターニングする手法。図のようにフォトレジストやポリイミドをストライプ形状でパターニングした後、Alなどのメタルをベタ蒸着する。この結果、メタル膜が上下でセルフパターニングされる仕組み。カソードラインのショートを回避するため、図のようにフォトリソで逆テーパー状でパターニングするのが一般的だ。
※ステラ・コーポレーションではディスプレイ製造向けとしてCAD/CAMソフトウェア「Stella Vision」、測長&外観検査装置「STシリーズ/LSTシリーズ」を製品化しています。 |
カレンダー加工
スクリーンメッシュの縦糸・横糸が交差する部分を圧延して平坦化処理する加工法。紗厚を薄くするとともにスキージの磨耗を低減するという役割がある。
|
起毛処理
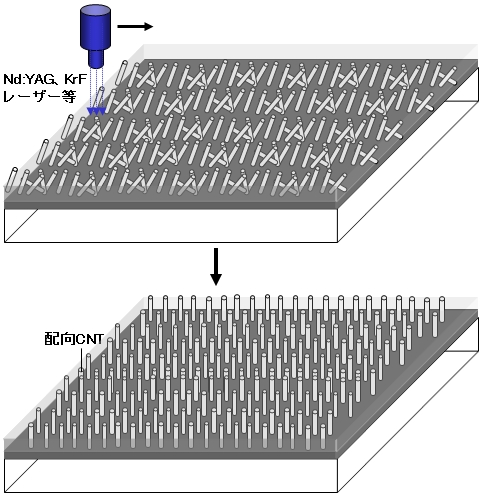 |
▲レーザー照射法によるCNTエミッタ起毛処理イメージ |
フィールドエミッションランプのナノカーボン系エミッタで適用される表面処理方法。表面露出、垂直配向などさまざまな呼び方があり、エミッタのエミッション特性を高めるため、寝ているエミッタを立たせる。とくに、塗布プロセスで成膜したシングルウォールカーボンナノチューブエミッタで必須とされる。
手法としては粘着フィルムラミネート法、レーザー照射法、サンドブラスト法、活性化処理法などが知られる。 |
CAD(Computer Aided Design)
コンピュータ支援設計のことで、コンピュータを用いて設計をすることを指す。CADシステムはコンピュータによる設計支援ツール。人の手によって行われていた設計作業をコンピュータによって支援し効率を高めるという目的から派生した言葉である<ウィキペディアからの引用を元に編集>。
※ステラ・コーポレーションではCAD/CAMソフトウェア「Stella Vision」を製品化しています。
|
CADデータ直接比較法
検査アルゴリズムのひとつで、その名の通り、撮像した実際のパターンと設計データであるCADデータを直接比較して合否を判定する。双方の違いが視覚的にとらえることができるため、量産だけでなく、研究開発用途にも最適な検査アルゴリズムといえる。
※ステラ・コーポレーションの測長&外観検査装置「STシリーズ/LSTシリーズ」はDRC法やCADデータ直接比較法といった複数の検査アルゴリズムを採用することにより検査精度を向上するとともに、検査時間の短縮を図っています。
|
共重合体ポリマー
2種類以上の低分子化合物(モノマー)を同時に重合させることで生成するポリマーで、コポリマー(copolymer)とも呼ばれる。
|
共蒸着
二つ以上の材料をそれぞれの蒸着源から蒸着させて基板上で混合膜を蒸着する成膜法。有機ELデバイスや有機薄膜太陽電池などの活性層を成膜する際に用いられ、図のようにホストと微量のドーパントを共蒸着する。 |
極性溶媒
液体を構成する分子が極性を持つため比較的大きな誘電率を持ち、イオン結晶や極性を持つ分子が溶解しやすい。水、アルコール、アンモニアなどがこれに当たる。
|
グラデーション膜
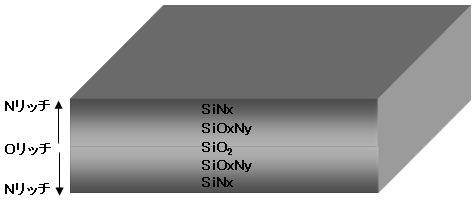
▲Si系ガスバリアグラデーション膜のレイヤー構成例 |
その名の通り、断面組成がグラデーション(傾斜)になっている膜。例えば、図のようにデバイスのSi系ガスバリア膜を成膜する場合、同じで主原料(ターゲット材またはCVD原料)を使いながら、ガス雰囲気やガス分圧を時間によって変化させることによりNリッチやOリッチといった傾斜組成膜を連続成膜する。
また、有機ELデバイスではキャリアトランスポートレイヤー〜発光層にも有効で、この場合、おもにホストマテリアルと複数のゲストマテリアルの蒸着比率をコントロールすることにより、ホストベースのグラデーションレイヤー(界面レス化ともいう)を成膜する。つまり、従来機能分離していた3層(例えばホール輸送層/発光層/電子輸送層)を実質的に1レイヤーにする。 |
グラビア版
グラビア印刷やグラビアオフセット印刷で用いる円筒状の版。彫刻のように、シリンダーの表面に溝パターンが刻まれており、まずここにインクを充填した後、ワークにインクを再転写して印刷する。この際、ワークに直接転写印刷する方式をダイレクトグラビア印刷(または単にグラビア印刷)、シリコンブランケットロールに転写した後、再びワークに転写する方式をグラビアオフセット印刷という。スクリーン印刷法に比べ高速で印刷できるほか、印刷解像度も比較的高く10μmクラスのファインパターンが印刷できる。その反面、設備が大掛かりになるほか、高精度グラビア版が供給できるメーカーが少ないことがデメリットといえる。
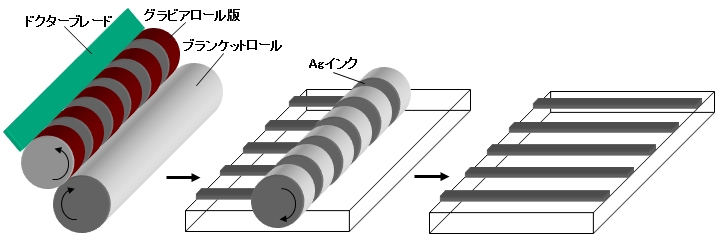 |
▲グラビアオフセット印刷のイメージ |
グラビア版の製造方法は、@中空構造のメタルシリンダーにCu膜などをめっき成膜する、Aフォトレジスト塗布〜レーザー直接描画〜現像し、これをマスキングパターンをしてめっき膜をウェットエッチングする、Bフォトレジストを剥離する、CDLC(Diamond Like Carbon)膜を全面に成膜して表面強度を高めるというレーザー描画+エッチング法が主流だが、あらかじめ金属触媒をフォトリソでパターニングしてからCu膜を自己整合的にめっき成膜するアディティブめっき法も適用可能だ。
※ステラ・コーポレーションではグラビア版製造向けとしてCAD/CAMソフトウェア「Stella Vision」、リベア装置「Repair Vision」、測長&外観検査装置「STシリーズ/LSTシリーズ」を製品化しています。
|
黒欠陥(ショート欠陥)
デバイス上のパターン欠陥で、本来はライン間にスペースがあるべきはずなのに、機能膜そのものの残存や異物などの付着によってライン間がつながってしまっている現象を指す。電極パターンではショート欠陥と呼ばれることが多く、これがひとつでもあると基本的にNG製品となる。このため、レーザービームを局所的に照射して除去するのが一般的である。
※ステラ・コーポレーションではリベア装置「Repair Vision」を製品化しています。
|
クロマトグラフィ処理
物質を分離・精製する方法のひとつ。物質の大きさ、吸着力、電荷、質量、疎水性などの違いを利用することにより、物質を成分ごとに分離する。
|
ゲル電解質
電解質は溶媒中に溶解した際に陽イオンと陰イオンに電離する物質で、イオンが電荷の担い手となって液体中を移動することにより電気を流す。固体電解質は固体中をイオンが移動できるもの。ゲル電解質はその中間的なもので、網目状になったポリマー分子のネットワーク中に液体電解質、すなわち溶媒(可塑剤)とイオンが存在し、イオンが移動することにより電気が流れる。
|
検査アルゴリズム
アルゴリズム(algorithm)は数学、コンピューティング、言語学などの分野において問題を解くための手順を定式化した形で表現したもの。検査アルゴリズムは外観検査のための方式論。
|
コーヒーステイン現象
インクジェットプリンティング法でインクをワーク上に塗布した際に起こる現象。コーヒー滴をこぼした時、滴の周辺部だけ色の濃いシミが残るため、コーヒーステイン現象と呼ばれる。乾燥過程で液の対流が起こり、周辺部の濃度が濃くなるために発生する。
|
サイドエッチング
ウェットエッチングプロセスにおいてオーバーエッチングされることにより、想定よりも線幅が細くなってしまう現象。線間のギャップ(スペース)が広い場合や、多層膜を同じエッチャントで一括エッチングする場合(膜によってエッチングレートが異なるため)に多く発生する。
※ステラ・コーポレーションではサイドエッチングを予測しCADパターンにあらかじめ補正をかけるエッチング補正機能を搭載したCAD/CAMソフトウェア「Stella Vision」を製品化しています。
|
錯体型ペースト・インク
インクやペーストといった溶液状態では導電性粒子レスでありながら、基板上に塗布し焼成すると、主成分である有機金属錯体のケミカル反応によってピュアメタル膜が得られるマテリアル。溶液状態ではメタル粒子フリーのため、酸化することがない。
|
SAM(Self-Assembled Monolayer)
有機TFTでは有機半導体の結晶性・配向性を高めるため、有機半導体膜を成膜する前にSAMによって配向処理するのが一般的である。SAM材料としてはフッ素化アルキルシラン、OTS(オクタデシルトリクロロシラン)、HMDS(ヘキサメチルジシラザン)、ODS(オクタデシルトリメトキシシラン)などが知られ、これらをゲート絶縁膜をはじめとする下地上に減圧成膜もしくは塗布する。
|
酸化還元反応
化学反応のうち、反応物から生成物が生ずる過程において原子やイオンあるいは化合物間で電子の授受がある反応のこと。酸化還元反応ではある物質の酸化プロセスと別の物質の還元プロセスが必ず並行して進行する。
|
酸素欠損
金属酸化物において酸素が抜けた結晶の欠陥を指す。IGZO-TFTをはじめとする酸化物TFTでは酸素欠損の発生を抑制するため、不活性ガスであるArに加え、O2ガスをパージして酸化物半導体膜を成膜する。また、IGZO半導体膜はO2ガス流量(5〜10sccm程度)によって電気導電性を制御する。
|
酸素プラズマ処理
強力な酸化力を有する酸素プラズマによって、おもに有機物(膜)を分解除去または表面改質させる処理方法。試料表面に高エネルギー状態の酸素ラジカルを照射する。有機TFTでは接触角を低下させることによる濡れ性の改善、表面仕事関数の調整などに用いられる。
|
サンドブラスト法
微細な研磨剤をワークに吹き付けて対象膜をドライエッチングする方法で、@DFR(ドライフィルムフォトレジスト)ラミネート、A露光、B現像、Cサンドブラスト、DDFR剥離、といったフローで処理される。つまり、Cの工程でコンベンショナルなウェットエッチングやドライエッチングの代わりにサンドブラストを用いる。サンドブラスト自体はガラスの曇り加工、金属部品などの洗浄・表面処理、かつらの毛の表面処理など幅広い用途で使われる。
エレクトロニクスデバイスでパターニング法として適用されたのはPDP(Plasma Display Panel)で、高さ100μm以上とハイアスペクト比構造物であるバリアリブをパターニングするために量産採用された。
最近では、有機ELデバイスの光取り出し効率を高めるため、ガラス基板自体をサンドブラストで切削処理して表面を荒らした後、高屈折率材料を塗布する方法も検討されている。
|
酸素分圧
大気中に含まれる酸素の圧力。エレクトロニクスデバイス製造プロセスでは酸化物などのスパッタリング成膜条件のひとつで、とくに酸化物半導体では酸素分圧によって電気伝導率などの特性が変化しやすいため、シビアに管理する必要があるとされる。
|
C12A7(12CaO・7Al2O3)エレクトライド
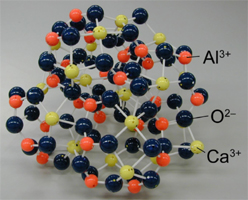 |
▲C12A7エレクトライド |
エレクトライドとは、陰イオンに代わって電子と陽イオンをイオン結合した化合物。C12A7(12CaO・7Al2O3)は、セメントの原料として使われるC12A7から酸素陰イオンを除去し、陰イオンとして機能する電子を内包させた籠状のナノサイズセラミックスで、セラミックスながら導電性があり、電子放出性も有する。結晶の仕事関数は2.4eVときわめて低く、さらに化学的に不活性という特徴がある。従来は1000℃以上で高温成膜して結晶化させる必要があったが、近年では室温でアモルファス膜が成膜できるなどエレクトロニクスデバイスに適用できる環境が整ってきた。
すでに多結晶のC12A7エレクトライドスパッタリングターゲットが開発されており、O2レス環境で室温成膜することができる。もちろん膜は透明で、アモルファス膜の仕事関数は3.1eVに過ぎない。
とくに有効とされるのがアモルファスIGZO-TFT駆動有機ELディスプレイで、Li系に代わる電子注入材料として注目されている。Nチャネルでのみ動作するa-IGZO TFTには既存の低温poly-Si TFTとは異なる積層構造、つまり逆構造トップエミッションがふさわしいためで、コンベンショナルなLiF電子注入層パネルに比べ優れたJ-V特性を示すとされる。 |
CMP(Chemical Mechanical Polishing)
文字通り、化学的かつ機械的にワークを研磨するプロセス。半導体でシリコンウェハーの平坦化処理に用いられ、CeO2などのCMPスラリーを用いながら研磨パッドを回転接触させて研磨処理する。
|
COG(Chip on Glass)
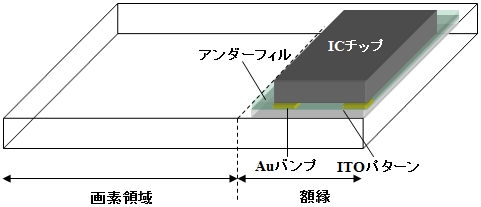 |
▲COGによる接続イメージ |
駆動用ドライバICとLCDパネルの接続方式のひとつで、ドライバICをダイレクトでガラス基板に実装する。ガラスというリジッドな基板にSiチップを直接載せるため、熱膨張などの観点からも相性がよく、部品点数削減、ハイスループットなど実装コストを大幅に削減できる。また、透明なガラスに接続するため、端子のアライメントも基板に色の着いたFPC方式に比べ容易だ。
その反面、 FPCを用いる他の2方式(TAB、COF)に比べ歩留まり、リペアの点では大きなビハインドを抱える。まず、歩留まりでは実装時の接続不良のほか、ICチップ自体の不良も考慮に入れなければならない。実装メーカーに納入されるICチップは良品を示す「KGD(Known Good Die)」の状態で供給されるが、100%保証されているわけではない。仮に不良チップを接続してしまった場合、これをガラス基板からはがしてリペアする手法も確立されていない。複数個を実装するケースではひとつの不良で1パネルを破棄しなければならないなど、歩留まりに影響するファクターの大きさが課題といえる。このため、比較的実装個数の少ない小型パネルへの採用がメインとなっている。
|
CDロス(サイドエッチング長)
エッチングプロセスでパターンにサイドエッチングが入る長さ(=幅)。
|
Sheet to Sheet方式
ガラス、シリコンウェハー、プラスチックフィルムといったサブストレートをシート状態で搬送して各種プロセスを行う方式。ロール状のフィルムを繰り出しながら連続的にプロセス処理するRoll to Roll方式と対峙する意味である。半導体やディスプレイデバイスの場合、これらシート状態のサブストレートをプロセス処理した後、複数枚カセットに収納してロボットで搬送し、次工程装置へ送る。
|
シード層
めっき成膜で種(シード)となる層。FPCではNiやCuなどをシード層として薄膜で成膜しフォトエッチング法でパターニングした後、Cuを自己整合的に無電解めっき成膜することにより膜厚を稼ぐ。いわゆるセミアディティブ法である。あらかじめ薄膜をフォトリソでパターニングするため、微細化・精度の面でサブトラクティブ法よりも有利である。
|
シランカップリング剤
分子内に有機材料と反応結合する官能基および無機材料と反応結合する官能基を同時に有する有機ケイ素化合物で、有機TFTの表面処理によく用いられる。具体的には、ゲート絶縁膜をシランカップリング剤でSAM処理すると、上部に成膜する有機半導体の配向性が向上しキャリアモビリティなどの特性が改善される。また、本来撥水性を有しているため、光パターニング処理によって下地を撥水・親水パターニングし、その後、塗布・印刷するメタルインク・ペーストの着弾精度を補完することができる。
|
シングルチャンバ・マルチソース方式
低分子有機ELデバイスにおける有機膜蒸着法のひとつ。ひとつのチャンバ内に有機材料用蒸着セルを5〜6個設け、ホール注入材料から電子輸送材料までを一貫処理する。この結果、チャンバ内の圧力や露点が変化せずにひとつのデバイスを処理でき、歩留まりが改善できるといわれる。
クラスターツール化する場合、複数のチャンバで基板をそれぞれパラレル処理する。1チャンバをメンテナンスしている最中も他のチャンバが稼働できるため、フレキシビリティが高いのも特徴となっている。 |
水素アブレーション
低温poly-Si TFTの作製プロセスにおいてプラズマCVD成膜したa-Siプリカーサ膜にはHが多量(約5at%)に含まれている。このため、エキシマレーザーアニール法で再結晶する際、膜の温度がSiの溶融温度に達するため、このHが気化して突沸し(水素アブレーション)、結晶化した膜を剥がしてしまう。水素アブレーションを防止するため、ELA処理前にN2雰囲気において400〜450℃熱処理してHを蒸発させる。こうした脱水素処理後のH量は約1at%程度まで低減される。
|
水中レーザーアニール法
低温poly−Si TFTでa-Siプリカーサを多結晶化する方法のひとつで、文字通り水中でエキシマレーザーをa-Siに照射する。
通常の空気中レーザーアニールでは空気中に拡散する熱エネルギーがSi膜中に拡散するエネルギーより低いためSiの表面で温度が高くなるのに対し、水中レーザーアニールではより多くの熱エネルギーが水中に拡散するため表面の温度上昇が抑制される。その結果、温度勾配が均一化され、サイトの数が低減することでグレインサイズが大きくなる。また、Si原子の気化が抑制され、溶解したSiが膜表面で凝集することもなくなる。これらの結果、膜の表面平滑性はプリカーサa-Si膜レベルをキープ。グレインサイズもエネルギー密度の上昇によって空気中レーザーアニールの3倍程度に増大するといわれる。 |
ステップカバレッジ
段差被覆性。成膜プロセスでよく使われる用語で、ステップカバレッジ性がいいと下地形状に関わらず均一な膜が成膜できる。つまり、下地の凹凸形状に沿った形で成膜される。薄膜成膜技術はCVD法とスパッタリング法に大別されるが、前者は後者に比べステップカバレッジ性が高い。
ちなみに、ステップカバレッジ性と対比する意味で使われるのがプラナリゼーション性。こちらは下地の表面形状に関係なく、成膜した膜の高さを全面にわたって一定に保つことを意味する。エレクトロニクスデバイスでは層間膜やプラナリゼーション膜の成膜で重要な特性である。
|
SGS(Super Grain Silicon):別名MILC(Metal-Induced Lateral Crystallization)法
a-Siプリカーサ膜を結晶化する方法のひとつで、とくにアクティブマトリクス有機ELディスプレイのTFT向けに適するとされる。
一般的に、低温poly-Si TFTはpoly-Siの作製にエキシマレーザーアニール(ELA)を用いるが、a-Siをpoly-Si化する際のレーザービーム強度バラつきがトランジスタのバラつきに直結し、有機ELDでは輝度ユニフォミティに影響する。また、poly-Si膜の表面平滑性が低いため、上部に形成されるゲート絶縁膜の絶縁破壊をもたらす危険がある。そこで、ポストELAとしてMetal-Induced Lateral Crystallization(MILC)、別名SGS(Super Grain Silicon)が開発された。
プロセスフローは、図のようにまずプラズマCVD法などでa-Siプリカーサ膜をガラス基板上に成膜する。次に、a-Si上にSiNx、SiO2、SiONといったキャップレイヤーを形成する。続いて、Ni粒子やNi-Siをスパッタ成膜する。この際、粒子状でNi原子が入射するが、キャップレイヤーがブロッキングするため、成膜後もNiはシリサイド化しない。その後、400〜590℃でアニール処理をするとNi原子はキャップレイヤーを通過してa-Si膜に到達する。この際、Ni原子は複数が集合してシリサイド化し、グレインサイズが大きくなりa-Siのシードとなる。最後に、再度熱処理またはELA処理するとシリサイド化したNiグレインは他のNiグレインと衝突するまで成長し、a-Siがpoly-Si化する仕組み。poly-Siのグレインサイズは10〜200μmにまで成長させることができる。また、表面平滑性も約1nmと高い。
ポイントはNi粒子のスパッタリング成膜方法で、このプロセスでpoly-Siのグレインサイズと密度が決まる。通常は基板を移動させながらスパッタリング成膜するため、基板移動速度とNiターゲットへの投入パワー密度が二大プロセスパラメータとなる。つまり、基板移動速度に比例してグレインサイズが大きくなる一方、投入パワー密度に反比例する形でグレインサイズが小さくなる。例えば移動速度を高速化すると基板へのプラズマ照射時間が短くなり、a-Siプリカーサ膜上に達するNiが減る。この結果、核生成のシードが減り、結果的にグレイサイズが大きくなる。一方、投入パワー密度を高めると、スパッタリングされるNi量が増える結果、グレインサイズが小さくなる。このため、グレインサイズを3〜130μmに制御することができる。
なお、コンベンショナルなELA法に比べグレインの質が落ち総じてモビリティも低下するため、ドライバ回路などの周辺回路をガラス基板上にビルトインする場合はその部分だけにグリーンレーザーなどを選択的に照射するなどの工夫が求められる。
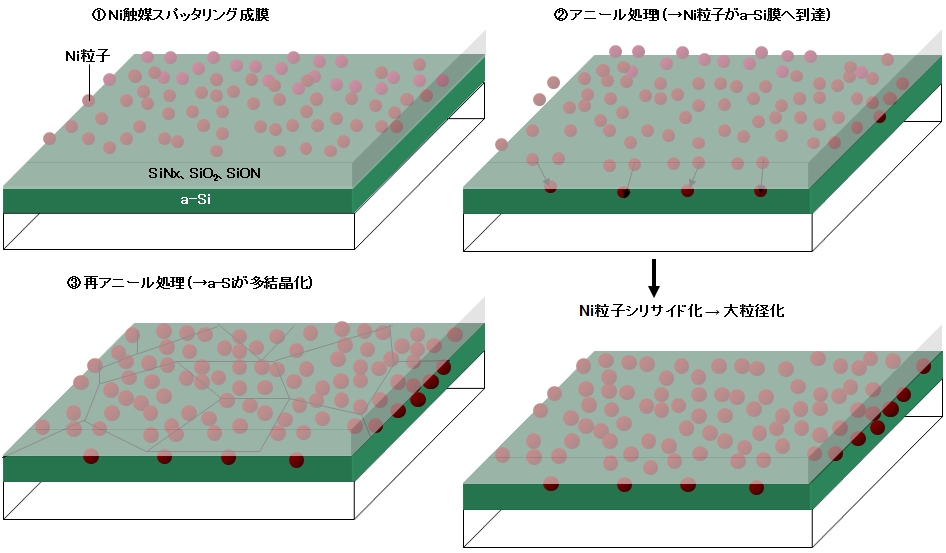 |
▲プロセスイメージ |
|
白欠陥(オープン欠陥)
デバイス上のパターン欠陥で、本来はつながっているべきラインにスペースが発生してしまっている現象を指す。電極パターンではオープン欠陥と呼ばれる。電極パターンではこれがあると即NGとなるが、絶縁層や電極間のチャネルなどでは致命的欠陥にはならない場合もある。リペア方法はピンやディスペンサによるリペア材料のスポット照射、またCVD(Chemical Vapor Deposition)方式による局所成膜法などが知られるが、いずれにしてもこれらオープン欠陥をリペアした後、その周囲をレーザー照射によって正確にカットするトリミング処理を行う場合が多い。
※ステラ・コーポレーションではリベア装置「Repair Vision」を製品化しています。
|
スクリーンマスク
エレクトロニクスデバイスの生産において代表的な印刷手法であるスクリーン印刷で用いる版。構造は図の通りで、Alなどの金属フレーム(中空構造)にポリエステルやSUS(ステンレス)をメッシュ状に一定のテンションをかけて紗貼りし、その上部に感光性乳剤を塗布してパターニングしたものである。機能性インクであるペーストは乳剤パターンの開口部からワーク上に押し出されて転写される。以前はSUSなどを直接フレームに接着する直貼りタイプが主流だったが、PDP(Plasma Display Panel)が量産化された1996年頃からパターニング用としてはコンビネーションタイプが主流となっている。
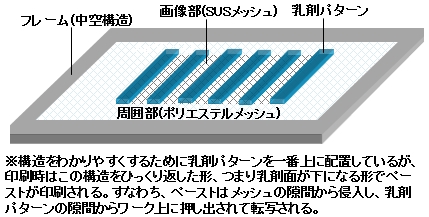 |
▲コンビネーションスクリーンマスクの構造 |
コンビネーションスクリーンは周囲のメッシュをポリエステルに、画像部(印刷エリア)を耐久性が高く伸びにくいSUSにする。容易に想像できるように、印刷を繰り返しても、言い換えれば圧力を繰り返しかけてもポリエステルワイヤーが印刷後に復元することによって画像部のSUSワイヤーが伸びにくくなり、耐久性、さらに経時変化に対する寸法精度(安定性)も向上する。もちろん、高価なSUSメッシュの使用量が減るというコストメリットもある。
従来、スクリーン印刷ではL&S=100μm程度が限界とされてきたが、PDPの量産化以降、印刷解像性が大幅に向上し、近年では30〜50μm幅のファインパターンが量産シーンでも実現。チャンピオンデータながら5μm幅というウルトラファインパターンも紹介されるレベルにまでなってきた。
なお、コンビネーションスクリーンマスクの製造方法は@フレームにポリエステルメッシュを紗貼りする、A画像部にSUSメッシュを紗貼りする、B画像部のポリエステルメッシュをカットする、C感光性乳剤を塗布する、D原版(フォトマスク)を用いて乳剤面をUV露光する、E現像によって非露光部を除去する、といった流れで、この後、測長や外観検査を経て出荷される。
※ステラ・コーポレーションではスクリーンマスク製造向けとしてCAD/CAMソフトウェア「Stella Vision」、測長&外観検査装置「STシリーズ/LSTシリーズ」を製品化しています。
|
スレッショルド(threshold)
日本語では閾値で、境界となる値。この値を境に上下で意味、条件、判定などが異なるような値を指す。電子回路の高電圧と低電圧の区別、プログラミングの条件判定などでしばしば用いられる概念。例えば、TFTでは動作電圧、ディスプレイでは発光開始電圧などでスレッショルドがよく用いられる。
|
素子分離
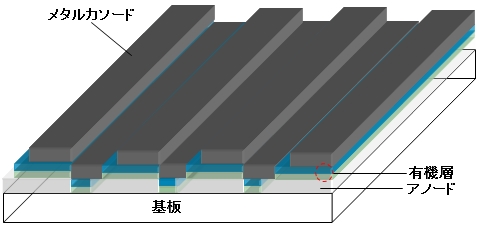 |
▲素子分離のイメージ |
有機薄膜太陽電池は数o角サイズという小型ならアノード、有機層、カソードともベタでいいが、大型化するとアノードの抵抗が大きすぎて発熱による電気エネルギーロスがあるため、極端に変換効率が低下する。そのため、素子を分離するケースが多い。この場合、選択肢は@インクジェットプリンティング(IJ)法、各種オフセット印刷法、メニスカスコーティング法で有機半導体材料をダイレクト印刷する、Aフェムト秒レーザービームなどを照射してベタ膜を短冊状にレーザースクライブする、のどちらかになる。ブランク部の幅は数十μmで、ピッチは10o程度と微細化する必要がなく、薄膜シリコン太陽電池と同様、それぞれのレイヤーを数十μmずつずらして分断加工する。 |
ゾル-ゲル法
各種の金属アルコキシドのアルコール溶液を出発材料にして加水分解・重縮合した後、熱処理によってゾルを経て、その固化体であるゲルを作製する方法。例えばシリカ(SiO2)をゾル-ゲル法で合成する場合、TEOSなどのアルコキシド(シリカ前駆体)を酸性または塩基性条件で加水分解・重縮合反応させることにより、アルコールを脱離させて合成する。
|
DLC(Diamond like Carbon)
炭化水素または炭素の同素体からなるアモルファスの硬質膜。水素含有量と、含まれる結晶質の電子軌道がダイアモンド寄りか、もしくはグラファイト寄りかによって性質が区別される。硬さはビッカース硬さ1500〜7000Hv。硬さ以外では潤滑性、耐摩耗性、化学的安定性、表面平滑性などに優れる。エレクトロニクス関連では、グラビアシリンダー版やグラビア印刷用ガラス版などの版の強度を高めるために用いられる。
成膜法はCVD法もしくはPVD(Physical Vapor Deposition)法で、前者ではアセチレンなどの炭化水素ガスをチャンバ内でプラズマ化し、気相合成した炭化水素をワーク上に成膜する。ワーク温度が室温〜200℃と低く、成膜レートも比較的高いため、現在もっとも多く利用されている。
他方、後者にはスパッタリング法やイオンプレーティング法などがあり、黒鉛原料を真空中でイオンビームやアーク放電・グロー放電にさらしてターゲットから叩き出した炭素原子を基板上に堆積させる。
|
対向ターゲットスパッタリング(FTS:Facing Target Sputtering)法
ターゲットを対向配置してプラズマを閉じ込め、Arガスによって叩き出されたスパッタリング粒子だけをワークに付着させる方法。プラズマスパッタによって発生した電子は2枚のターゲット間をマグネットによる磁力線に巻きつきながら往復するため電離効率が向上し、高密度プラズマが両ターゲット間に生成される。
最大のアドバンテージは磁力線によってプラズマがターゲット間に収束されるため、ワークには電子や負イオンが入射せず、プラズマフリーでスパッタ成膜できること。このため、電子やイオン衝撃に対しセンシティブな有機デバイス向けとして有望とされる。さらに、成膜温度も低温化できる。ターゲットのエロージョンが全面均一になり、ターゲット利用率が40%程度と高いのも特徴だ。一方、成膜レートはコンベンショナルなスパッタ法の6〜7割と低い。
ディスプレイデバイスでは、トップエミッション構造有機ELデバイスの光透過性カソードに有効で、このケースではすでに形成されてある有機層にダメージが少なくなる。 |
TEOS
オルトケイ酸テトラエチル(Tetraethyl orthosilicate)の略。Si(OC2H5)4化合物で、中心のSiO44-イオン(オルトケイ酸イオン)にエチル基が四つついた構造をとる。
エレクトロニクスデバイスのSiO2絶縁膜用原料ガスとしてよく用いられ、200℃以下の低温でプラズマCVD成膜することができる。真空チャンバ内でO2ガスと反応させることによりSiO2膜にする。
|
DRC(Design Rule Check)法
主要な検査アルゴリズムのひとつで、あらかじめ決められたルールに基づいて検査の合否判定を行う。つまり、半導体やPCBなど生産するデバイスによってそのルールは大きく異なり、あらかじめデバイスメーカーが決めたルールを外観検査装置にインプットし、これに応じて検査装置で自動検査する。
※ステラ・コーポレーションの測長&外観検査装置「STシリーズ/LSTシリーズ」はDRC法やCADデータ直接比較法といった複数の検査アルゴリズムを採用することにより検査精度を向上するとともに、検査時間の短縮を図っています。
|
TMA(トリメチルアルミニウム)
液体状の有機金属化合物で、分子式は(CH3)3Al。CVD法やALD(Atomic Layer Deposition)法でAl2O3膜を成膜する際によく用いられる。大気中では不安定なため、不活性ガス雰囲気で取り扱う必要がある。
|
Tg(ガラス転移点)
固体結晶を加熱すると融点で液体に変わりはじめ、固体と液体が共存する間は温度が融点に維持され、固体がすべて液体に変わるとその温度が上昇する。
非晶質の固体を加熱すると、低温では結晶並みに硬く流動性がない(粘度が測定不能なほど大きい)固体が、ある狭い温度範囲で急速に剛性と粘度が低下して流動性が増す。この際の温度をガラス転移点という。ガラス、プラスチックフィルム、有機材料などの耐熱性を示す指標としてよく用いられる。
|
電荷移動錯体
2種類以上の分子からなる分子間化合物のうち、電荷移動相互作用を有するもの。電子供与性分子と電子受容性分子を混合した場合、電子供与性分子から電子受容性分子に部分的な電荷移動が起こり、その結果、電荷を帯びた分子同士が軌道相互作用や静電相互作用などの引力によって錯体を形成する。
有機分子でありながら電気伝導性や超伝導性を有するものがあり、有機導電性材料としてはTTF(テトラチアフルバレン)をドナー、TCNQ(テトラシアノキノジメタン)をアクセプターに用いてTTF-TCNQ導電膜を形成する手法が知られる。
|
電子写真印刷法
電子写真印刷法の基本原理はコピー機やレーザープリンターと同じだが、エッチングレジスト機能を持つ液体トナーを用いた静電転写方式を採用している点が異なる。図のように帯電〜露光〜現像〜リチャージというフローによってワークに電圧を印加せずに印刷転写する仕組み。ポイントとなる液体トナーは粒径0.5μm以下の微粒子を使用。塩化第二鉄や塩化第二銅に対する耐エッチャント性と苛性ソーダなどに対する剥離性を付与。現状のFPC製造プロセスを変更することなく、DFRラミネート〜露光〜現像工程を印刷工程1回に削減できる。容易に想像できるように、印刷速度も2m/min以上と速く生産性が高いのが特徴となっている。
※ステラ・コーポレーションではFPC製造向けとしてCAD/CAMソフトウェア「Stella Vision」、測長&外観検査装置「STシリーズ/LSTシリーズ」を製品化しています。
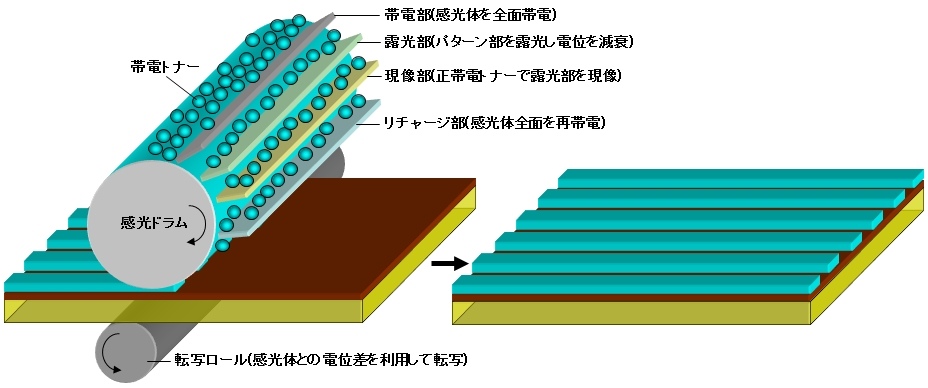 |
▲プロセスイメージ |
|
デンドリマーホスト
高分子燐光有機ELデバイスの燐光発光材料として期待されているホスト材料。例えばコアをIr系燐光基、周囲のデンドロンにホール輸送基をつけ、アルキル鎖でこれらをつなげた多機能型燐光性デンドリマーが知られる。デンドリマー構造にすることによって燐光基同士の相互作用が抑制され、効率低下をもたらす濃度消光が低減できることが期待できる。 |
テンティング法
テンティング法は、サブトラクト法で両面PCBを製造する際に用いられる手法。基材にスルーホールを開けた後、Cuを両面にめっき成膜し、サブトラクト法でパターニングするが、テンティング法ではスルーホールをエッチャントから保護するため、スルーホール上部に当たる部分のドライフィルムフォトレジスト(DFR)を残して“テント”を張る。そして、露光〜現像〜エッチングが終わった段階でDFRを剥離する。テンティング不良はDFRによって形成したテントが破れてスルーホール内断線が発生すること。
※ステラ・コーポレーションではPCB製造向けとしてCAD/CAMソフトウェア「Stella Vision」、測長&外観検査装置「STシリーズ/LSTシリーズ」を製品化しています。
|
突起欠陥
周辺に比べ極端に膜厚が厚くなり、突起物のようにみえる欠陥を指す。とくに問題となるのは平滑性が要求される膜で、絶縁膜、Si膜、マイクロカラーフィルターのRGB着色層などではリペアが必須となる。リペア方法はテープ研磨やレーザー照射が一般的である。
※ステラ・コーポレーションではリベア装置「Repair Vision」を製品化しています。
|
凸版反転オフセット印刷法
凸版反転オフセット印刷法は一般的なオフセット印刷法を改良したメソッド。最大の違いは、図のように版胴から版に余分なインキを転写し、残ったインキパターンを基板に転写することにある。この結果、版でのインキ残りが発生せず、XYZ方向の印刷精度を低下させる“糸引き現象”がなくなる。このため、オフセット印刷法よりも印刷精度が高いといわれる。
ウィークポイントは版に転写したインキを現時点では再利用できないことで、このためいまのところアディティブプロセスとは言いにくいのが実情だ。
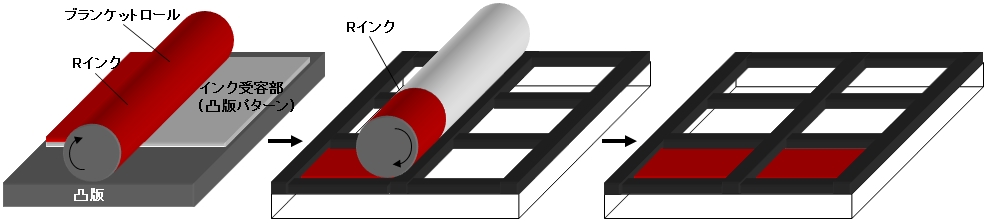 |
▲凸版反転オフセット印刷法によるCFパターニングイメージ |
|
DPN(Driver Per Nozzle)
インクジェットヘッドのノズルを駆動するシステムのことで、それぞれのノズル毎に吐出量や吐出速度を制御する。このため、ノズルの口径や形状のばらつきにも個々に対応でき、全体としては原理的にまったく同じノズルを用いてIJ印刷することになる。
|
ナノインプリンティング法
フォトリソ法などで微細な溝パターンを設けたスタンプ(型)を基板上の樹脂膜などに押しつけて転写成形してパターニングする方法。nmオーダーの微細パターンが得られるため、ナノインプリンティング法と呼ばれる。また、成形した膜をどのように硬化させるかによって熱ナノインプリンティング法と光ナノインプリンティング法に分かれる。
|
ナノサイズ効果
物質を数十nm以下の大きさにシュリンクすると、量子効果と呼ばれる特殊な現象が発現する。つまり、従来なかった新たな機能が発現したり、従来に比べ特性が大幅にアップする。こうしたコンセプトからナノテクノロジーの採用機運が高まった。
エレクトロニクスデバイスの配線材料としてよく用いられるナノメタルインク・ペーストでは、メタル粒子を従来のμmサイズから10nm以下にナノサイズ化することにより粒子の表面が活性化し、融点が降下する融点降下効果が得られる。例えば、本来Agの融点は961℃だが、ナノサイズ化すると200℃以下で焼結し基板上でグレイン同志が融着して膜になる。このため、耐熱性の低いプラスチックフィルムや紙にこれらのインク・ペーストを印刷できるわけである。
|
ナノメタルインク・ペースト
粒径数十nm以下のナノメタルパウダーを主成分にしたメタルインク・ペースト。低温焼成できるほか、インクジェットプリンティング法ではノズル目詰まりがないという利点がある。
容易に想像できるように、ナノメタル粒子は表面が活性であるため、容易に凝集する。このため、インク・ペーストの製造過程ではまずナノメタル粒子に有機保護膜をつける。この結果、溶液やインク・ペースト状態では凝集せずに独立分散状態を保つ。そして、基板に塗布後、焼成することによって有機保護膜が一部バーンアウトし、ナノメタル粒子同士が融着して膜となる。いうまでもなく、この有機保護膜のバーンアウト率が導電性を左右するため、比抵抗と焼成温度はトレードオフの関係になる。
|
軟化点
固体物質を加熱していく際に、物質が軟化し変形しはじめる温度。
|
濡れ性
基板や下地に対しフォトレジストなどの塗布液が塗布しやすいかを言い表した言葉。これには被塗布面の接触角が大きく影響し、接触角が高い、つまり撥液性と高いと濡れ性が悪くなり、接触角が低いと、つまり親液性が高いと濡れ性がよくなる。有機TFTをはじめデバイスで濡れ性を改善するにはUV照射や酸素プラズマ処理といった表面改質処理が有効で、こうした処理後、フォトレジストなどの塗布液を塗布する場合が多い。また、フォトレジスト自体にフッ素系界面活性剤などの撥液材料を微量添加すると、濡れ性が改善されることもある。
|
濃度消光
濃度が高くなると、分子間相互作用により発光が減衰する現象。有機ELデバイスでは発光ドーパントのドープ比率を多くすると、この現象が発生する。このため、発光ホストに対するドーピング比率は10wt%以下にするのが一般的。
|
背面セルフアライン露光
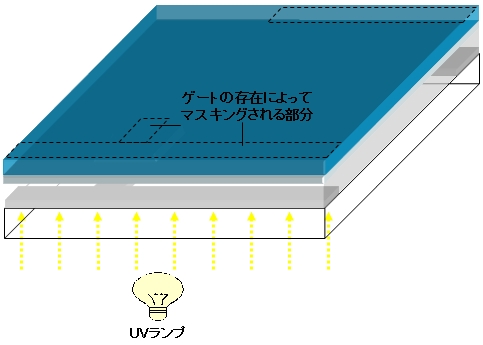 |
▲背面セルフアライン露光のイメージ |
各種TFTで用いられる露光方式。もっとも有名なのはボトムゲート型TFTのゲート電極をセルフアラインマスクにするプロセスで、例えばエッチングストッパー型酸化物TFTのエッチングストッパーを形成する場合、酸化物半導体を成膜しフォトレジストを塗布した後、フォトマスクレスでガラス基板の裏側から露光光を照射する。この際、露光光はガラス基板を透過するが、ゲート電極がある部分は透過しない。このため、ゲート電極がマスクの役割を果たし、ゲート電極の上部にあるフォトレジストは露光されない。したがって、現像〜エッチング〜レジスト剥離工程を経ても、エッチングストッパーがゲート電極上部にセルフパターニングされる。 |
ハーフトーンマスク
バックチャネル型a-Si TFTを4枚マスクプロセスで作製する際に用いる特殊フォトマスク。半透過領域を持ったフォトマスクで、通常のバイナリーマスクの透過率が100%と0%の二つであるのに対し、グレーの領域を持たせた3段階(100%、半透過、0%)の透過率で露光光を制御し、厚みの異なるレジストパターンを1回のフォトリソ工程で形成する。つまり、ハーフトーンマスク1枚で従来のバイナリーマスク2枚分の機能を果たす。
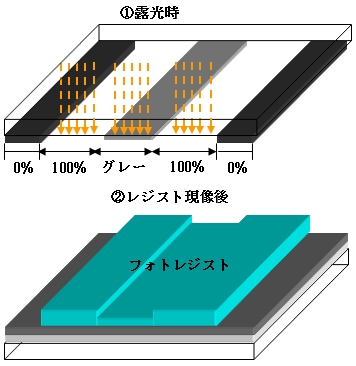 |
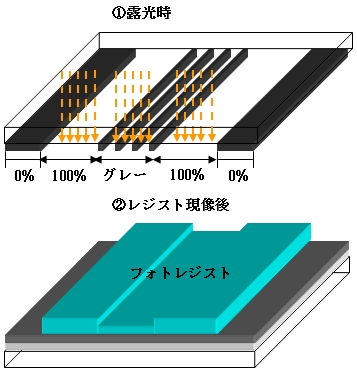 |
▲スタックドレイヤータイプ |
▲スリットタイプ |
ハーフトーンマスクは図のように半透過領域をスリットパターンで形成するタイプと、半透過膜で形成するタイプがある。
スリットタイプ(別名グレースケールマスク)は、露光光の透過率を微細なスリットパターンで制御する。スリットパターンはTFTアレイ用露光装置の解像度(3〜4μm)を下回る微細さが要求され、光の干渉効果と回折効果で透過率をコントロールする。配置するスリットの本数とパターン幅は要求される透過率ターゲットによって決まる。TFTのチャネル部といったクリティカルなエリアでは1μm幅のスリットを1〜2本配置する。通常のバイナリーマスクと同じCr膜を用いるため、製造プロセスは微細なパターニングを施す以外、通常のバイナリーマスクと同じで、成膜もCr1回、レーザー直描パターニングも1回で済む。このため、リードタイムも短い。
一方、スタックドレイヤータイプは半透過膜そのものの透過率によって中間調領域を形成する。半透過膜はCrOx膜を膜厚40nm程度で成膜するか、もしくは通常のCr膜を10nm程度で薄膜成膜する。スリットタイプのように光の回折などを考慮して細かいパターンをデザインする必要がなく、設計に対する負荷の小さい点が長所といえる。ただし、製造プロセスはバイナリーのCr膜と半透過膜で2回の成膜とパターニングが必要で、2回目のパターニングでは厳密なアライメント精度が要求される。このため、リードタイムも手間がかかる分だけ長くなる。
|
PANエッチャント
燐酸(H3PO4)、硝酸(HNO3)、酢酸(CH3COOH)からなる混合エッチャントで、Alなどのメタル膜のウェットエッチングによく用いられる。IGZO-TFTをはじめとする酸化物TFTの酸化物半導体層は総じて酸に弱いため、ソース/ドレイン電極をウェットエッチングする場合はあらかじめ半導体膜を保護するエッチングストッパーを設けておくか、またはドライエッチングでパターニングする必要がある。
|
光配向
LCDのポリイミド配向膜を一定方向に配向させる方法で、この結果、液晶分子が配向する。UV光に反応する配向膜材料に偏光した光を斜めから照射して非接触で配向させる。光の照射角度や照射量によって液晶分子の配向状態(プレチルト角、アンカリングエネルギーなど)を制御できる。また、非接触方式であるため基本的に歩留まりが高いほか、下地である画素電極の膜厚依存症がないなど表面凹凸性に関係なく均一な配向性が得られる。
その反面、液晶材料の配向性が低く、さらに配向膜材料の光配向特性が不十分なため、高い光照射エネルギーが必要になるなど、コンベンショナルなラビング配向に比べ生産性が低いといった弱点を抱える。
ただし、近年では光反応性の高い配向膜材料の使用や光配向プロセスの改善によって量産適用のアナウンスが相次ぐなど、従来の問題は解消されつつある。 |
非感光性エッチングペースト
文字通り感光性がないエッチングペースト。このため、各種印刷法によってダイレクト印刷してエッチング用マスキングパターンを形成する。
|
P3HT
poly(3-hexylthiophene-2,5-diyl)の略。代表的なp型半導体ポリマーで、溶剤に溶解するため、塗布型有機薄膜太陽電池の半導体層に用いられる。バルクヘテロ接合型ではn型半導体であるPCBMと混合して塗布されることが多い。
|
PDMS(dimethylpolysiloxane)
紫外線硬化タイプの液状シリコーンゴム。PDMS製モールドはマスターモールドから加工する際の再現性が高く、離型性に優れ、さらにナノポーラス構造であるため溶媒が蒸発しやすいため、ナノインプリント法、マイクロコンタクトプリント法、オフセットスクリーン印刷法といったファイン印刷法のスタンパとして用いられる。
|
PEDOT/PSS
ポリエチレンジキオシチオフェン/ポリスチレンスルホン酸の略。代表的な導電性ポリマーで、フレキシブル透明電極のほか、ホール注入特性に優れるため有機ELのホール注入層に用いられる。塗布液は青みがかっており、膜の透明性と比抵抗はトレードオフの関係となる。耐食性が非常に高いため、ウェットエッチング法でパターニングするのは困難で、基本的には各種塗布法や各種印刷法で成膜される。
|
ヒロック
メタル膜で熱工程を経た後に発生する突起物。Al系膜でよく観察される。ヒロックの発生を抑制するため、TFTの配線プロセスではAlにNdやNiを数wt%添加したAl合金がよく用いられる。
|
ピンホール欠陥
膜中に針でつついたような穴ができた現象を指す。広義では白欠陥に分類される。電極パターンでは完全に断線していない限り問題にならない場合が多い。一方、ディスプレイの画素電極やマイクロカラーフィルターでは大きさによってはリペアが必要になったり、NGになったりするケースもある。
|
フォトマスク
半導体、ディスプレイ、MEMS(Micro Electro Mechanical Systems)、プリント基板(PCB)、リードフレーム、タッチパネルなどのデバイスを作製する際に、フォトリソグラフィ技術を用いてファインパターンを作製するのに不可欠な原版。
具体的には、フォトレジストまたは感光性ペーストの塗布・硬化後(あるいはドライフィルムフォトレジストラミネート後)、露光工程でUV光などの露光光をフォトマスク越しに照射する。この際、ポジ型フォトレジストの場合、露光光が照射された部分が現像液に可溶化。一方、ネガ型フォトレジスト、感光性ペースト、ドライフィルムフォトレジスト(DFR)の場合、露光光が照射された部分が現像液に不溶化する。このため、露光後の現像工程で照射部もしくは未照射部が溶解メカニズムによって除去されてマスキングパターンが完成する。銅箔、シリコン膜、メタル膜などをパターニングする際はフォトレジスト塗布前にこれらを基板上に成膜しておき、現像後のエッチング工程でマスキングパターンをマスクにしてエッチングする。そして、最後にフォトレジストをリフトオフメカニズムによって剥離する。一方、感光性ペーストはそれ自体にAg(銀)などの機能性材料が内包されているため、塗布・硬化〜露光〜現像〜焼成という4工程でパターニングされる。
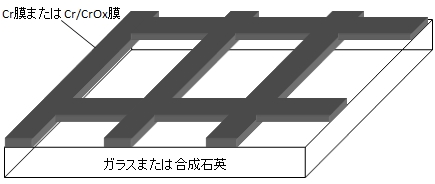 |
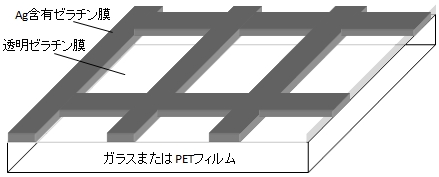 |
▲クロムマスクの構造 |
▲エマルジョンマスクの構造 |
基板 |
PET |
ソーダライムガラス |
低膨張ガラス |
合成石英 |
熱膨張係数 |
1.8×10-5/℃ |
8×10-6/℃ |
4×10-6/℃ |
6×10-7/℃ |
軟化点 |
160℃ |
740℃ |
900℃ |
1600℃ |
|
表1 フォトマスク基板の熱膨張係数と軟化点 |
フォトマスクはパターニングするデザインルールによって複数の種類に分類される。まずサブストレート(基板)からは合成石英、低膨張ガラス、ソーダライムガラス、PET(ポリエチレンテレフタレート)フィルムが用いられれる。表のように、熱膨張係数は基板によって大きく異なり、それにともなって温度に対する寸法安定性が変化する。いうまでもなく、デザインルールがシビアなデバイスでは合成石英や低熱膨張ガラス、PCBやタッチパネルのようなデザインルールが比較的穏やかなデバイスではソーダライムガラスやPETフィルムがマスク基板として用いられる。他方、露光光の遮光膜はCr膜またはCr/CrOx積層膜と写真乳剤(ハロゲン化Ag含有エマルジョン乳剤)が用いられ、前者はクロムマスク、後者はエマルジョンマスクといわれる。容易に想像できるように、パターン解像性、耐久性、扱いやすさでは前者が大きく上回っており、上記のサブストレートとの組み合わせによってデザインルールのシビアなデバイスに用いられる。他方、後者はソーダライムガラスまたはPETフィルムとの組み合わせで作製され、それぞれエマルジョンガラスマスク、エマルジョンフィルムマスクと呼ばれる。
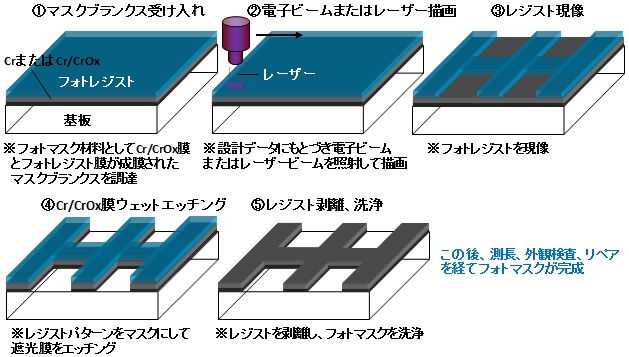 |
▲クロムマスクの製造フロー |
フォトマスク(半導体向けはレチクルと呼ばれる)はクロムマスクの場合、@スパッタリング法でCr膜またはCr/CrOx膜を成膜、Aポジ型フォトレジスト塗布・硬化、B電子ビーム描画またはレーザー描画、Cフォトレジスト膜現像、D遮光膜ウェットエッチング、Eフォトレジスト膜剥離といったフローで作製される。デバイスの製造と異なるのは基本的に露光工程または描画工程で、フォトマスク製造フローではCAD(Computer Aided Design)データを元に電子ビームまたはレーザービームを一筆書きのメカニズムで照射してレジスト膜をパターニングする。当然、フォトマスク生産ラインでもっとも高価な装置が描画装置であり、億円単位での投資が必要になる。なお、PCBはフォトマスクと同様、露光工程を描画工程に置き換えたレーザー直接描画で製造されるケースもある。一方、エマルジョンマスクの場合、@ハロゲン化Ag含有ゼラチン膜塗布、Aレーザー描画、B現像といったフローで作製される。
クロムマスクでは@とAを成膜専業メーカーが行うことが多く、@とAが完了した状態をクロムマスクブランクスと呼ぶ。他方、エマルジョンマスクでは@が塗布された状態を乾板と呼び、富士フイルムなどの写真感材メーカーがフォトマスクメーカーに供給する。
ところで、フォトマスクを用いてファインパターンを作製する場合、パターニング精度は描画装置の解像度>フォトマスクの解像度>デバイスパターンの解像度と、プロセスフローが進むにつれて精度が劣化する。このため、解像性・精度・寸法安定性はフォトマスク基板の種類と描画装置の解像度によって決まると考えていい。
※ステラ・コーポレーションではすべてのフォトマスク製造向けとしてCAD/CAMソフトウェア「Stella Vision」、クロムマスク向けとしてリベア装置「Repair Vision」、エマルジョンフィルムマスク向けとしてレーザー描画装置「SilverWriter」、自動現像装置、ガラスライクフィルムエマルジョンマスク製造装置を製品化しています。
|
プッシュコート法
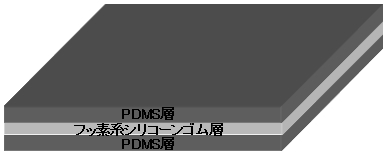 |
▲スタンプの構造 |
プッシュコート法は塗布型有機半導体膜向けの開発された塗布プロセス。プロセスフローは、@スタンプ圧着による塗布型半導体膜の形成、Aスタンプによる溶剤吸収とそれにともなう薄膜成長、Bスタンプリリース、という3段階からなる。
図のように表面層にPDMS層(両面)、中間層に溶剤浸透を遮断するフッ素系シリコーンゴム層からなる3層構造スタンプを使用。このスタンプは表面平滑性が高く、溶剤吸収にともなう歪みが小さい。このため、溶剤を数分かけてゆっくり吸収し、しかも表面付近に保持する。すなわち、スタンプ表面の“半濡れ”状態が持続するため、スタンプ-薄膜間の固着力は基板-薄膜間の固着力に比べ常に弱く、薄膜を基板表面に残したままスタンプがリリースされる。剥離後はスタンプから溶剤が徐々に脱離するため、スタンプを繰り返し使用することができる。
有機TFTは液体をはじく絶縁膜表面に有機半導体膜を形成すると特性が安定化する。しかし、従来の塗布法では撥水面によって溶液がはじかれるため、材料ロスが大きくなり、また均質な薄膜が得られにくい。これに対し、プッシュコート法は撥水性のゲート絶縁膜上にも均一に塗布することができ、この結果、キャリアモビリティをはじめとする特性も向上する。
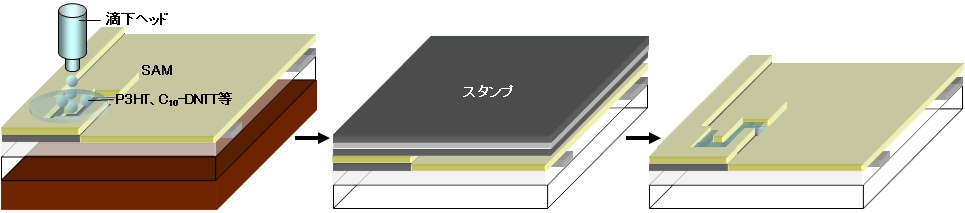 |
▲プロセスイメージ |
|
フラックス(flux)
物質を融解しやすくするために添加される物質。
|
プリンタブルエレクトロニクス(別名プリンテッドエレクトロニクス)
インクジェットプリンティング(IJ)法、スクリーン印刷法、グラビアオフセット印刷法、凸版印刷法などの各種印刷法でエレクトロニクスデバイスを作製することをいう。別名プリンテッドエレクトロニクスともいう。
従来の真空成膜+フォトリソ法に比べ、@常圧プロセス、A必要な量の材料だけを使用する(エッチングレス)、B比較的低温プロセス、C工程数が材料印刷〜硬化だけと少ない、D省スペース、といったコストメリットがあり、さらに少量多品種生産にも対応しやすい。とくに有効とされるのは有機TFT、有機ELディスプレイ、有機薄膜太陽電池、色素増感太陽電池、電子ペーパーデバイス、FPCなどで、これらをプリンタブルエレクロニクス技術で生産できれば劇的なコストダウンが図れるとされる。
※ステラ・コーポレーションではプリンタブルエレクトロニクス向けとしてCAD/CAMソフトウェア「Stella Vision」、測長&外観検査装置「STシリーズ/LSTシリーズ」、リベア装置「Repair Vision」を製品化しています。
|
プレチルト
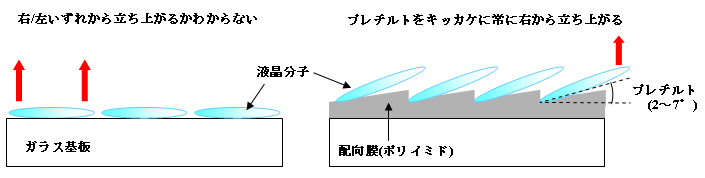 |
▲プロセスイメージ |
LCDでは電場をかけて寝ている液晶を起こす際、両端のいずれか一方を頭にして立ち上がらせる必要がある。プレチルトは図のように液晶分子を傾ける際、どちらか一方を頭にして立ち上がるようなキッカケづくりをする。
図の左のようにプレチルトがない場合、液晶分子の立ち上がりは右からと左からの二通りに分かれる。すると傾きが互いに逆になるリバースチルトが存在することになり、コントラストが低下するなど光学特性に不都合が生じてしまう。プレチルトはこの問題を防ぐ役割を果たす。
配向膜にポリイミドを用いてラビング処理をすると、自然に2〜7°のプレチルトをつけることができる。ラビング処理を必ず一方向で行う理由はここにある。
|
フロー・コーティング法
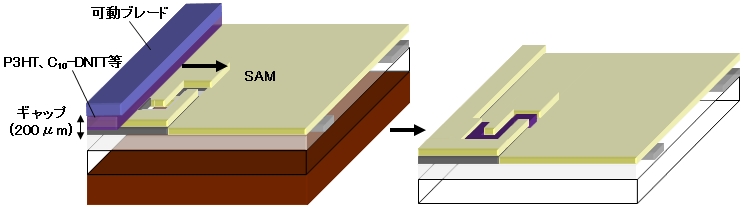 |
▲フロー・コーティング法による有機半導体塗布イメージ |
フロー・コーティング法は、基板の上部に可動型塗布ブレードをわずか上方に傾けてセットし基板と200μm程度のギャップを確保。その空隙に溶液を注入した後、塗布ブレードを平行移動させることによって膜を配向させながら塗布する仕組み。低沸点溶液が塗布できるほか、スピンコート法に比べ材料利用率が高く、少量の試料で実験ができる。とくに有効なのは塗布型有機半導体層で、有機半導体分子は配向成長するため、チャネル長方向に対して平行に掃引するとモビリティが向上するといわれる。 |
プロセスウィンドウ
別名プロセスマージン。これが広いとデバイス製造プロセスのマージン(許容範囲)が大きくなり、製造しやすくなる結果、歩留まりも向上する。
|
フロート法
建築、自動車用ガラスの製造に広く用いられている横引き製法で、溶解したSnを溜めたフロートバスに溶解したガラスを流し込むことで板状のガラスを成形する。フロートバスは1000℃以上に電熱されており、融点232℃のSnは風呂(バス)の中の湯のような状態となっている。流し込まれたガラスは比重の重いSnの上に浮き(フロート)、表面張力によって薄く平らに拡がる(ちなみにガラスの比重は2.48、Snは7.3)。これを徐令室で少しずつ冷やし固化させた後、超硬工具で切断する。
考案したのは英Pilkingtonの社主アラステア・ピルキントン氏。夕食後の皿洗い中に皿の上の水に油が浮くのをみてひらめいた。
フロートバスと徐冷室はそれぞれ50m以上もあり、ゆっくりと徐冷できるため寸法安定性に優れる。出口側でガラスを引く速度を速めることで薄型化でき、逆にせき止めるように制御して厚みをつける。
|
ペリクル
ハードクロムマスク用防塵フィルム。とくに投影式露光機を用いて露光する際に有効で、フォトマスクへのパーティクル付着を防止。フォトマスクの洗浄回数が低減できるなどメンテナンスが容易になる。
|
ポリシラン
ケイ素-ケイ素結合を有する化合物の総称で、一つのケイ素-ケイ素結合から百万単位の結合まで多数の化合物が知られる。最大の特徴はケイ素-ケイ素σ結合間に共役多重結合に似たσ共役が観測されること。つまり、ポリシランはSi-Si主鎖による紫外吸収および発光性を示し、ポリシランの鎖長が長くなるにつれて吸収波長および発光波長が長波長側へシフトする。
|
マイクロコンタクトプリント法
マイクロコンタクトプリント法(μCP法)は、PDMS(ポリジメチルシロキサン)製などのあらかじめ作製したモールドにインクをつけた後、モールドをサブストレートに接触させてインクを転写する仕組み。つまり、ハンコの原理で転写・印刷する。そのメカニズムから用いるインクは数十cpsと中粘度にする必要があり、アライメント時間を除き5分程度で転写処理が完了する。近年、その印刷解像度は飛躍的に向上し、5μm以下というファインパターンも得られている。
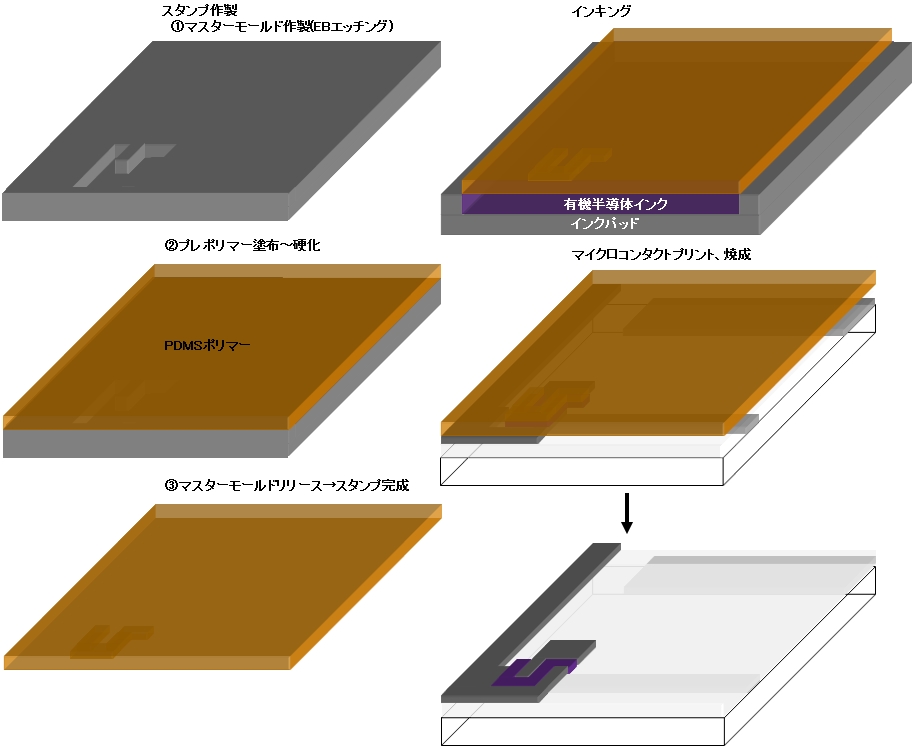 |
▲マイクロコンタクトプリント法による有機半導体層形成イメージ |
|
マイクロレンズアレイ(MLA)
ロッドレンズを束ねてアレイ状にしたものや、マトリクス状にレンズをアレイ状に面加工したものを指す。アレイ状に設ける微細構造物のディメンジョンは光の波長以下に微細化するのが一般的。ディスプレイデバイスの光利用効率を改善する光学フィルムに多く用いられる。加工法としてはナノインプリント法や、微細ボールを用いた自己整合的プラズマエッチング法などが知られる。
|
無機配向
LCDでは、コンベンショナルなポリイミド膜に代わって無機膜を用いる場合がある。無機膜の代表例としてはDLC(ダイヤモンド・ライク・カーボン)が挙げられる。DLC膜は水素原子を含んだアモルファス状のカーボン膜で、ハードディスクの耐摩耗膜としても用いられている。膜質は堅く、化学的にも安定した絶縁膜であり、LCD用配向膜としては10nm前後の膜厚で形成される。通常はスパッタリング法またはCVD法で成膜され、膜の制御性ではポリイミド膜よりも優れているとされる。
|
無極性溶媒
その名の通り、極性を持たない分子からなる液体。このため、誘電率が小さく、無極性分子の溶解性が高い。ベンゼン、ヘキサン、四塩化炭素などがこれに当たる。
|
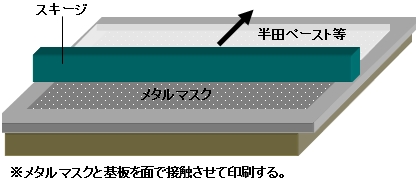 |
▲メタルマスクを用いた印刷のイメージ |
メタルマスク
メタルマスクは、おもにPCBの表面実装(SMT)用として半田ペーストを印刷する際に用いられてきた。金属プレートを開口パターニングしたメタルマスクを基板上に置き、ペーストをスキージで押し出して開口部からワーク上へ転写する。広義ではスクリーン印刷になるが、通常のスクリーン印刷がスクリーンマスクとワーク間に一定のギャップ(クリアランス)を設けながら線接触で印刷するのに対し、メタルマスクを用いた印刷ではメタルマスクとワークを面で常時接触させて印刷する。
メタルマスクの製造方法は要求される印刷解像度によってレーザー加工法、ウェットエッチング法、アディティブめっき法の3種類に分かれる。レーザー加工法とエッチング法ではおもにSUSが用いられ、前者はレーザーを照射することによりメタルプレートをダイレクト加工する。後者はいわゆるフォトエッチング法で開口加工する。これに対し、アディティブめっき法はフォトリソグラフィで金属触媒をパターニングした後、NiやNi-Co合金などの本材料を自己整合的にめっき法で積み増してプレート化する仕組みで、もっとも解像性が高く、エッチングメタルマスクのようなサイドエッチングが発生することもない。その反面、厚板化が難しく、ハンドリングを筆頭に扱いにくいというデメリットもある。
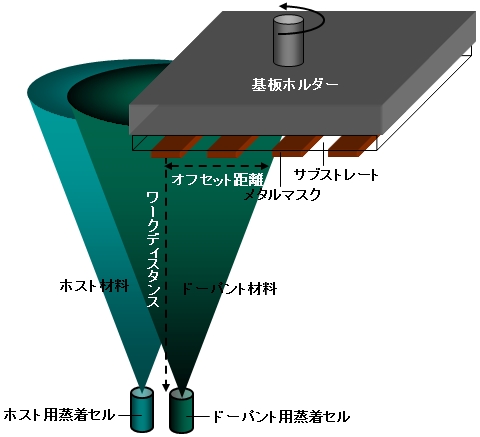 |
▲マスクスルーパターニング法のイメージ
(ステラ発行のCD-ROM「絵で見る有機ELディスプレイ製造プロセス」より引用) |
前記のように、メタルマスクはおもに半田ペーストの印刷に用いられてきたが、最近ではタッチパネルのドットスペーサの印刷や半導体のバンプの印刷などにも用いられるようになってきた。
さらに、スマートフォンのハイエンドモデルに搭載されている低分子有機ELディスプレイではこれまでとはまったく異なる用途で使用されるようになっている。図のように、RGBそれぞれの有機発光材料をメタルマスクの開口部からスルー蒸着するマスクスルーパターニング法で、このフィールドでは従来の要求精度とは次元の違うハイテクニックが求められる。このため、製造方法はアディティブめっき法とウェットエッチング法に限定される。プロセス上の課題は多く、この工程がフルカラーパネルの歩留まりを決めるという声すらあるほど。具体的には、まずメタルマスクにはパターン寸法精度、開口部のテーパー化、表面平滑性、洗浄性、高ヤング率、テンション均一性などが求められる。一方、プロセス面では基板とメタルマスクのアライメント精度、蒸着レート均一性、マスクの熱変形対策などが課題となっている。
※ステラ・コーポレーションではメタルマスク製造向けとしてCAD/CAMソフトウェア「Stella Vision」、リベア装置「Repair Vision」、測長&外観検査装置「STシリーズ/LSTシリーズ」を製品化しています。 |
メニスカスプリンティング法
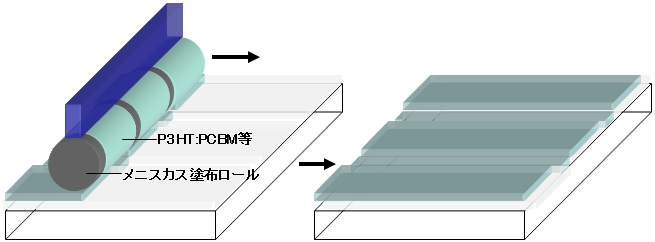 |
▲バルクヘテロ接合半導体膜の塗布イメージ |
図のように、基板と非回転のアプリケーター間にギャップ(100〜800μm)を設け、アプリケーター全面に保持されているインクをメニスカス効果によって転写するプロセス。特徴は@比較的厚膜でも膜厚ユニフォミティが高い、A低粘度インクが使用可能、という2点で、塗布膜厚はギャップ、印刷速度、インク濃度、インク粘度などによって制御する。有機薄膜太陽電池のバルクヘテロ接合半導体層の塗布プロセスなどに提案されており、図のようにラフパターンならパターニングも可能なため、アノード、有機層、カソードをずらして形成する“素子分離処理”をする必要がないとされる。 |
面蒸着法
低分子有機ELデバイスにおける有機膜蒸着法のひとつ。文字通り面型の蒸着源を用いた成膜法で、図のようにニードルバルブ型蒸着セルをチャンバ外に配置し、ホットパイプ、そして蒸着孔を設けたマニホールドを介して蒸着材料をチャンバ内へ導入し、上部に配置したワークに入射させる仕組み。マニホールドには蒸着孔が設けられており、蒸着材料は面形状で蒸発する。このため、材料利用率が向上するだけでなく、基板が大型化しても膜厚ユニフォミティが低下しない。
さらに分岐管を設けることによって有機層を1チャンバ内で連続蒸着することもできる。この場合、二つの材料の通り道となるホットパイプは例えばホール注入材料とホール輸送材料、またTgが近い材料同士で共通化。気になるコンタミネーションもないといわれる。この結果、1チャンバでひとつの材料を蒸着する従来のクラスターツール方式に比べ基板搬送時間が大幅に短縮でき、タクトタイムも1/2近くに短縮される。もちろん、デバイス上におけるコンタミネーションの危険も大幅に低減する。 |
誘電損失
電熱の一種で、交流電界を誘電体に加えた際、交流電界より位相が遅れて分極が起こるために発生する熱エネルギー。
|
陽極酸化
電解質溶液中に金属を浸し金属を陽極(正極)として通電すると、金属が酸化されて陽イオンとなり溶液中に溶解するか、表面で水の電気分解が起こり水素イオンと酸素ガスが発生する。金属を陽極として通電した場合に酸化物として残る場合を陽極酸化と呼ぶ。
エレクトロニクス分野では、陽極酸化によって自己整合的に微細凹凸構造アレイを形成するプロセスが検討されている。例えば、Alプレートを陽極酸化すると上部にポーラスAl2O3(アルミナ)が作製される。また、TFTでTaゲート電極を用いる場合、陽極酸化によって表面だけをTa2O5にしてゲート絶縁膜にすることができる。
|
ラテラル成長法
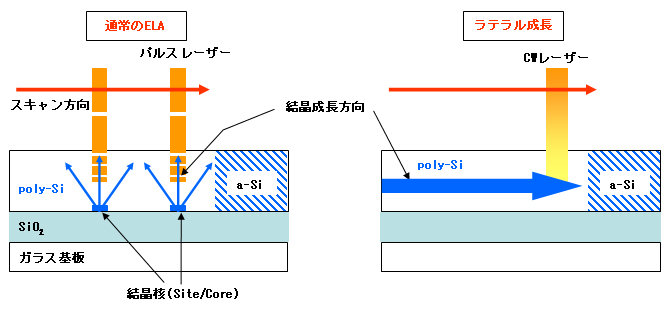 |
▲結晶化方法の違い |
ラテラル成長法(Lateral Crystallization)は文字どおり横方向に結晶を成長させる手法で、低温poly-Si TFT製造プロセスにおいてa-Siプリカーサ膜を結晶化する際に用いられる。コンベンショナルなエキシマレーザーアニール(ELA)の場合、図のように熱の吸収が表面から始まり、表面から下に向けて溶け出し、下側から冷却が始まって下から上に向かって凝固していく。このため、横方向に成長する時間がなく、グレインサイズは膜厚に律則される。パルスレーザーの冷却スピードは10億℃/秒と、非常に速いため横方向に成長する時間はほとんどない。急激な冷却は結晶の核をあちこちに発生させてしまうため、結果として大きな粒径が得られない。
上記したELAのウィークポイントをカバーすべく提案されているのがCW(Continuous Wave)レーザーによる再結晶化技術。結晶核から横方向にレーザーを引っぱることにより大粒径化させるコンセプトで、数十μmのグレインが得られる。レーザーの変動幅がELAに比べ小さく安定しているため、制御しやすく、横方向に温度勾配をつけた照射が可能になる。 |
ラビング配向
LCDのポリイミド配向膜を一定方向に配向させる方法で、この結果、液晶分子が配向する。液晶分子を配向させたい方向に向かって、配向膜の表面を機械的に擦る手法で、ドラムにベルベットのような1〜2mmの毛足を持った布を巻きつけ、回転させながら基板上を通過させる。布の巻き方、擦る際の毛あたりの強さが表示品質に影響を与えるとともに、布の均一性やラビングローラの偏芯、振動、基板ステージの平行度、剛性などでラビングの不均一性を生じ、表示ムラを引き起こすことがある。 |
リジダイズドスクリーンマスク
SUSメッシュにNiを電鋳することで強度を高めたスクリーンマスク。
|
リフトオフプロセス
コンベンショナルなフォトエッチングプロセスと対比されるプロセス。フローは@フォトレジストを塗布〜露光〜現像してパターニングする、Aメタル材料などの機能性膜を成膜する、B残ったフォトレジストを剥離する、という仕組みで、Bの工程でフォトレジストの上部に成膜された機能膜がレジストとともに剥離される。
パターニング解像性はフォトエッチング法に比べ劣り、基本的にはSnO2やAuといったウェットエッチングしにくい材料を用いる場合やR&Dで使用される。
|
量子ドット(QD:Quantum Dot)
量子ドット蛍光体は粒径nmサイズの化合物半導体粒子で、発光波長は粒径サイズによって自在に制御できる。また、nmサイズの量子閉じ込め効果によって高い吸収係数を確保しているため、輝度向上と消費電力低減が実現できる。
QDは、一般的にコアとシェル(殻)によって構成されるコア-シェル型材料を用いる。これは、コアオンリー材料に比べ発光強度が向上するため。ポピュラーなのはコアをCdベース、シェルにZnS系にしたCd-ZnS系で、発光色はコアサイズとシェルの組成成分によって設定する。例えば赤色と緑色はコアサイズ6〜8nmで、赤色はCdSeコア+CdZnSシェル、CdSeコア+CdS/ZnSシェル、波長520〜580nmの黄緑色材料はCdZnSeコア+CdZnSシェルを用いることが多い。一方、コアをZnリッチにするとバンドギャップが広がり、青色発光が得られる。青色QDの粒径は約10nmで、CdZnSコア+ZnSシェルが知られる。つまり、前記のように色調整がきわめて容易といえる。
他方、エコロジー面からCdフリーQDの開発も進められており、エコフレンドリーなInPをコアにしたInPコア+ZnSシェルや、InPコア+ZnSe/ZnSマルチシェル(発光波長555nm)などが開発。近年はトラディショナルなCdコアデバイスに近い発光特性が得られている。
|
良品比較方式
AOIの検査アルゴリズムのひとつ。写真のように、良品基板から良品データを作成し、比較検査を行う方式で、CADデータが支給されていない製品にも対応可能。 |
レーザードライエッチング
その名の通り、レーザービームを照射して機能膜を除去してパターニングすること。CADデータにもとづいて一筆書きのメカニズムでパターニングする。容易に想像できるように処理速度は遅いが、機能膜成膜〜レーザードライエッチングとわずか2工程でパターンが作製できる。このため、R&Dや試作などに有効だ。
※ステラ・コーポレーションのリベア装置「Repair Vision」はリペアのほか、レーザードライエッチング装置としても機能します。
|
ロータリースクリーン印刷
円筒状のギアにロータリースクリーンマスクをセットし、その内側からペーストをスキージングして転写・印刷する手法。プラスチックフィルムやメタル箔といったフレキシブルサブストレートをRoll to Roll方式で高速印刷できるというメリットがある。
元来、ロータリースクリーンマスクはNi電鋳メッシュが用いられてきたが、近年ではフラットスクリーンマスクと同様、SUSメッシュとエマルジョン乳剤を組み合わせた製品が登場するなど、FPCをはじめとするエレクトロニクスデバイスで採用機運が高まっている。
|
Roll to Roll方式
ロール状のフィルム(基板)を連続的に繰り出し&巻き取りながら各種膜を成膜&パターニングすることによりデバイスを生産する方法。容易に想像できるように生産性がきわめて高いため、大量生産に有効。とくに単層膜から3層程度の多層膜の成膜に適しており、各種機能性プラスチックフィルムの成膜によく用いられる。
反面、生産設備が大掛かりになるほか、少量多品種生産には適していないというデメリットもある。さらに、露光工程など高精度なアライメントが必要な工程には不向きである。このため、Roll to Roll方式の変形として搬送を連続で行い、露光などのプロセス時は静止状態でフィルムを処理するタクトタイム送り方式もよく用いられる。
従来、Roll to Roll方式はプラスチックフィルム専用の生産システムだったが、近年は100μm以下という超薄型ガラスも登場。このフレキシブルロールガラスをRoll to Roll方式で処理することも提案されている。
|
|