富士電機アドバンストテクノロジーは独自のAdvanced-CCM方式低分子有機ELディスプレイの最新成果として2.8型QVGAパネルを開発、「SID 2008」で披露した。a-Si TFT駆動、逆構造トップエミッション、ピュアブルーEL+CCM、インクジェットプリンティングCCMと最新テクノロジーをふんだんに盛り込んだパネルで、これによりアクティブCCMパネルの要素技術を完成。実用化へ向けて、後は事業化のGOサインを待つのみとなった。研究部隊のトップである木村浩有機EL開発部長を直撃した。
電子デバイス技術センター 有機EL開発部長■木村浩氏
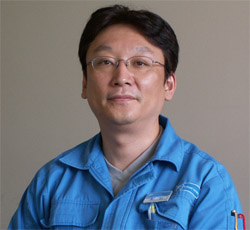 |
▲木村浩氏 |
Q:SID 2008でアクティブ駆動の2.8型QVGAパネルを披露されました。以前はパッシブパネルとアクティブパネル双方を開発されていたと認識していますが、アクティブパネルの開発に特化したと考えていいですか。
A:それで結構です。以前はパッシブパネルを中心に開発してきましたが、1年前にアクティブパネルに専念することにしました。ご承知のように、近年、パッシブパネルはLCDとの競争によって価格が急落。今後も数量自体は増えるものの、単価下落によって金額的には市場規模は横バイで推移するとみられるためです。
Q:有機ELDのカラー化方式のひとつであるCCM(Color Change Media)方式も以前から変わっているようにみえますが。
A:はい。初期は青緑EL発光を赤色CCMで赤色、緑色CCMで緑色に変換して効率を高めてきました。その後、白色EL発光+CCMにもトライ。また、R-CCMだけをマスクスルー蒸着する白色EL発光+CCMパネルも試作してきました。これら試行錯誤の結果、いきついたのがピーク波長460〜470nmのピュアブルーELを用いるEL+R-CCM/G-CCMパネルです。
Q:そのメリットは。
A:まずはEL発光層がホストと1ドーパントというシングルレイヤーで形成できるため、輝度面内均一性を高めやすく、寿命も高めやすいことです。従来の白色ELは青緑発光層と橙色発光層を2層化していたため、それぞれシビアな膜厚均一性、シビアなドーパントレシオが問われ、大型基板を歩留まりよく生産できるかについては自信が持てませんでした。
二つ目は、ピュアブルー発光をCCMで色変換するのがもっともロスが少ないためです。ピュアブルーEL発光はR-CCMを通過する際、赤色スペクトルをほぼ100%透過し、これ以外のスペクトルのうち70%程度を赤色に変換します。G-CCMも同様で、60%程度という変換効率が得られます。釈迦に説法ですが、類似カラー化方法である白色EL+CF方式とはこの点が決定的な違いで、効率面で圧倒的に有利といえます。もちろん、チャンバ数も発光層は1個、有機層トータルでも4個になりますので、その分プロセスコストを削減できます。
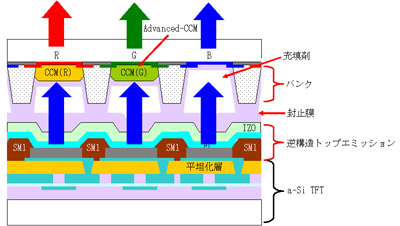
図1 アクティブ駆動Advanced-CCMパネルの構造 |
Q:ピュアブルー材料はホスト、ドーパントとも市販のものですか。
A:材料メーカー各社から市販されているものを使っており、特殊なものではありません。
PNドーピングで効率向上&電圧低減
Q:最新パネルの構造は。
A:背面基板上にa-Si TFT、反射カソード、有機EL層、透明アノード、パッシベーションを形成。一方の前面基板上にはカラーフィルター(CF)&ブラックマトリクス(BM)、R+G-CCM、パッシベーションを形成。これら両面基板をオイルである充填剤を介して貼り合わせた逆構造トップエミッションです。ちなみに、シール層とSi系パッシベーションによってガスバリア性が高いため、乾燥材レスです。
Q:アクティブ基板にa-Si TFTを用いたということですが、その理由は。
A:ご承知のように、当社が自らアクティブ素子を開発しているわけではないため、正直いってアクティブ基板の開発は外部任せになります。今回のa-Si TFTも当社で設計し、外部へ作製を委託しました。a-Si TFTと低温Poly-Si TFTにはそれぞれ一長一短があり、パネルの仕様に応じてチョイスする考えで、とくにa-Si TFTにこだわっているわけではありません。
Q:というと、特定のアクティブ基板メーカーとタイアップしているわけじゃないんですか。
A:違います。乱暴な言い方ですが、陳腐化した旧世代TFT-LCDラインを保有しているLCDメーカーは結構ありますから(笑)。
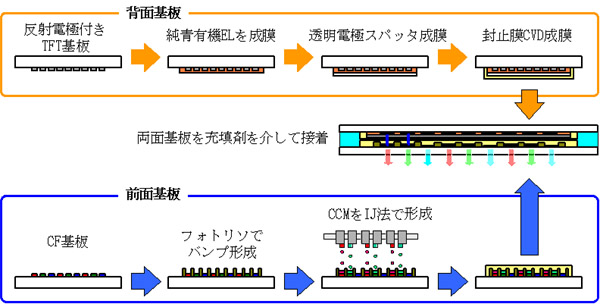
図2 Advanced-CCMパネルの製造フロー
|
Q:回路構成は。
A:スイッチングTFT、ドライビングTFT、ストレージキャパシタに加え、補償回路を1〜2個設けています。トップエミッション構造なので、開口率が低くても問題ありません。
Q:有機ELDではa-Si TFTは輝度均一性が高い反面、Vth(しきい値電圧)が大幅に変動するのが問題になっていますが。
A:おっしゃるとおりです。このため、補償回路を設けていますが、それでも低温Poly-Si TFT並みの安定性は望めません。実用化に当たっては、このあたりをさらに改善する必要があると考えています。
Q:次に反射カソード&画素電極の種類は。
A:Ag合金をスパッタリング成膜し、フォトリソでパターニングしています。いうまでもなく、Agは反射率が高いため、EL発光を効果的に反射させて前面基板側へ取り出すことができます。ちなみに、カソードの上部にはAgの腐食をブロッキングするためのプロテクトレイヤーを設けています。
Q:有機EL層ですが、電子注入層〜電子輸送層〜ピュアブルー発光層〜ホール輸送層〜ホール注入層という構成ですか。
A:個別の材料は申し上げられませんが、そういう構成です。ホール注入層はホストとF4-TCNQを共蒸着、電子注入層はホストとCsやLiなどのアルカリドーパントを共蒸着したpnドープ型にしています。この結果、効率が向上するとともに駆動電圧も低減します。
Q:話の腰を折るようですが、pnドーピングはドイツの会社の特許になっているのでは。
A:その会社のオリジナル材料を使えば特許に抵触すると思いますが、さきほど申し上げたように使用しているドーパントはごく一般的なものです。このため、そうした懸念はないと思います。
Q:有機EL層上に設ける透明アノードは従来と同様、IZO(In2O3-ZnO)ですか。
A:そうです。一般的なスパッタ法で成膜しますが、有機EL層へのダメージを抑制するため、ホール注入層の膜厚とスパッタ条件をオプティマイズしています。
Q:具体的には。
A:それはノウハウなのでちょっと・・・・・・。
IJ法によるCCM形成は比較的容易
Q:一方、CCM基板ですが、まずRGB-CFとBMを形成するわけですね。
A:そうです。コンベンショナルな顔料分散法で形成します。続いて、ネガ型フォトレジストを塗布、露光、現像してバンクを形成します。ここまでは一般的なフォトリソテクノロジーです。この後、従来はCCMをフォトリソで形成していましたが、今回初めてIJ法で形成しました。
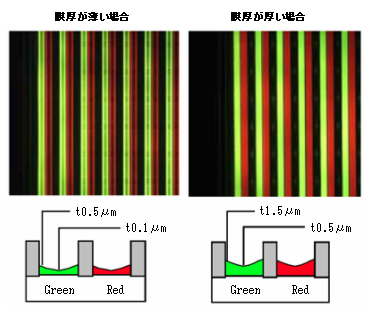
図3 CCMの膜厚の違いによる視認性比較 |
Q:R-CCMインク、G-CCMインクの材料は。
A:申し訳ありませんが、インクの組成については一切答えられません。IJ装置も市販装置を改造したもので、ハードにも当社のノウハウが活かされています。
Q:蛍光色素を分散したインクという解釈でいいですか。
A:それはそれで結構ですが、インクにもさまざまな種類がありますから(笑)。
Q:IJ処理を行う前に下地であるCFを親水化処理、バンクを撥水処理するんですか。
A:まず前者については、そのような必要はありません。ご承知のように、3色独立発光方式の高分子パネルなどではRGB発光層をIJ法でパターニングする際、ドット内で膜厚がバラつくと、それがそのまま輝度の差になって認識されます。このため、膜厚数十nmという世界で±数%というきわめて高い膜厚ユニフォミティが要求されます。これに対し、CCM層ではさほどの膜厚均一性は要求されません。具体的には、従来は図3のように膜厚を0.5μm程度に設定していました。このため、適当にIJ処理をすると、ドット中央部と端部では膜厚差が大きくなり、結果的に視認性に影響を及ぼします。これに対し、膜厚を1.5μmにしたところ、図3のように視認性が変化せず、膜厚依存性がきわめて少なくなることがわかりました。これは、膜厚が0.5μm以上ならば色変換効率はほとんど変わらないためです。つまり、高分子パネルのRGB発光層に比べ、比較的プロセスが容易といえます。
Q:ということは、IJプロセス時はXY方向の着弾精度にだけ注意すればいいわけですか。
A:“だけ”というと語弊があるかもしれません、イメージとしてはそんな感じです。膜厚均一性にさほど注意する必要がないとなれば、後はインクを安定吐出し、XY精度に気をつければいいということになります。
Q:そこで、さきほどの質問になりますが、バンクの撥水処理は。
A:それはケース-バイ-ケースで、プラズマ処理などによって撥水処理するケースもありますし、あらかじめ撥水性を有しているバンク用レジストを用いることもありますが、mustというわけではありません。
Q:そもそもインクの液滴サイズは。
A:現在のIJ装置は14pLです。今後、2.8型QVGA以上の高精細パネルを試作する場合はもっとも小滴対応のIJヘッドを使う必要があるでしょう。
Q:IJヘッドはノズル毎に印加電圧などのプロセス条件を自動制御するドット・パー・ノズルですか。
A:すいません。それは把握してません。要は再三申し上げてきた理由からIJ法によるCCMのパターニングはさほど難しくないということです。
Q:となると、IJ処理後の乾燥もさほど気を使わなくていいわけですか。
A:乾燥温度をいうとインクがある程度特定できてしまいますのでいえませんが、前記の理由から多少の乾燥ムラがあっても問題ありません。
Q:IJ法によるCCM形成のメリットは従来のフォトリソに比べプロセスコストだけですか。
A:もちろん、最大のアドバンテージはコスト面にありますが、それだけではありません。いうまでもなく、従来の蛍光色素分散レジストはUV感光用の光重合開始剤や光硬化剤が含有されており、総じて耐熱性が高くありません。これに対し、IJインクにはそうしたものが含まれてませんので、CCMの耐熱性や耐光性を高めることができます。これは、その後の工程であるSi系パッシベーションの成膜温度の制約が少ないことを意味しますし、インク組成によってはプラズマダメージが少ないものもあります。また、正直に申し上げてフォトリソで作製したCCMは耐光性が低いため、むしろEL発光層よりも劣化が早く、加速試験では300時間で色ずれを起こすことがありましたが、今回のIJ-CCMではそのようなことがなく、EL層よりも耐久性が高いことを確認しています。
Q:いずれにしてもIJ法によるCCM形成プロセスを確立したとなると、CFとBMもIJ法でパターニングすることも可能では。
A:まだトライはしてませんが、十分可能だと思います。
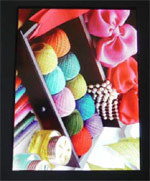 |
▲2.8型QVGAパネル |
Q:その場合、撥水性のあるBMを形成した後、RGB-CFを形成し、さらにRとGのCCMをIJ法で形成すればかなりの工程短縮になりますね。
A:そうなれば理想的ですね(笑)。
Q:ところで、IJ印刷速度は。
A:それもシークレットです(笑)。
Q:今回試作した2.8型QVGAパネルのスペックは。
A:1670万色のフルカラー表示で、輝度は150cd/m2、コントラストは10000:1以上です。色再現性はNTSC比80%です。
Q:有機ELDとしては色再現性が低いように感じますが。
A:ご指摘のとおりで、G-CCMインクがイエローがかっているのが原因です。ただ、色純度の高いG-CCMインクが完成していますので、これを使えばNTSC比100%になる見通しです。
中大型パネルに照準
Q:最後に貴社富士電機アドバンストテクノロジーの管轄外の話になりますが、製品化計画は。
A:それについては研究開発会社である私どもから申し上げられません。というより、ここで私がいっても説得力がありません(笑)。事業化の是非は富士電機本体が判断することになりますので。
Q:ただ、技術ロードマップはあると思いますが。
A:それに関してはある程度お答えすることができます。アクティブパネルに特化した以上、やはり大型パネルを実用化したいですね。また、富士電機という会社の体質を考えると、リスクの大きい携帯電話は避け、自社の自動販売機や産業用機器、さらに車載機器などのアプリケーションを想定しています。
Q:大型化とはどのあたりのサイズを指しているんですか。
A:既存の試作設備は200×200oですので、当面は7型クラスを目指しています。もちろん、事業化となれば370×470oや550×650o対応ラインという話も出てくるでしょう。
|